June 19, 2023
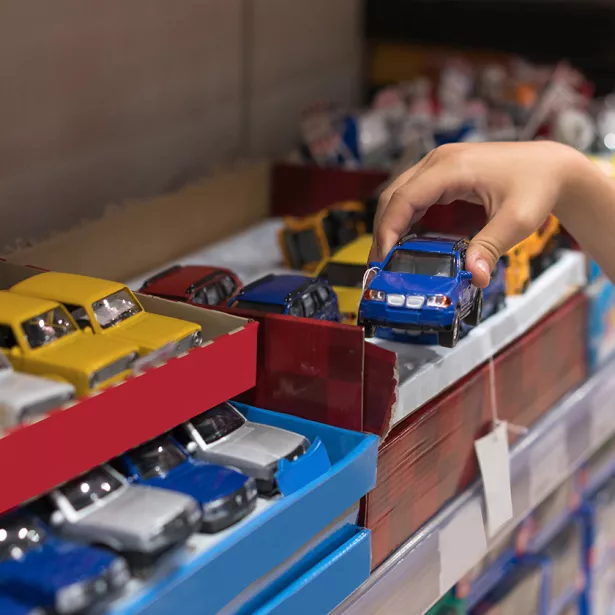
Safeguarding products with customized design and safety reviews
Despite extensive regulations and safety requirements, kitchen appliances continue to be a source of injury — particularly to children — and a leading cause of residential fires in countries around the world. While newer appliances often feature smart advanced safety features such as timers and automatic shutoff functions, many are also running faster and hotter than those of the past, frequently with little or no user oversight.
The pace of new product and feature development is getting faster too. Manufacturers are under increasing pressure to keep up with high production volumes while covering supply chain shortages, raising the risk of defects. Take the case of a U.S. electrical pressure cooker that passed compliance testing but had an undetected manufacturing error on the lid. Under certain circumstances, the lid opened prematurely, expelling hot food contents and posing a burn hazard.
The complexity and high number of components in the average appliance sold today increases its risk potential.
New or trending appliances that offer novel functions or cooking methods may not be fully covered by the most recent standards and regulations — even with strong compliance testing in place. Air fryers, for instance, which became popular in the mid-2010s and now represent a $900 million global market, have seen recalls across several brands, as both consumers and companies work to understand their characteristics.
To address as many risks and use conditions as possible, customized design and safety reviews are the smart choice for detecting mechanical, electrical, and thermal hazards in a kitchen appliance before it is introduced to the market. This can help prevent user injuries, financial loss, reputational damage, and product recalls.
Multicomponent appliances carry multifaceted risks
The complexity and number of components in the average appliance sold today increases its risk potential. For example, an item as basic as a toaster may include sensors, an actuator, control hub, and various user-interaction functions controlled by printed circuit board assemblies (PCBAs). PCBAs themselves can be vulnerable to design flaws and manufacturing errors that lead to electrical failures, apart from any issues with wiring.
Off-the-shelf components are another important consideration when designing appliances. Off-the-shelf components can create opportunities to streamline production time and control costs, but it can also be difficult to verify whether each off-the-shelf component has undergone a thorough design and safety review.
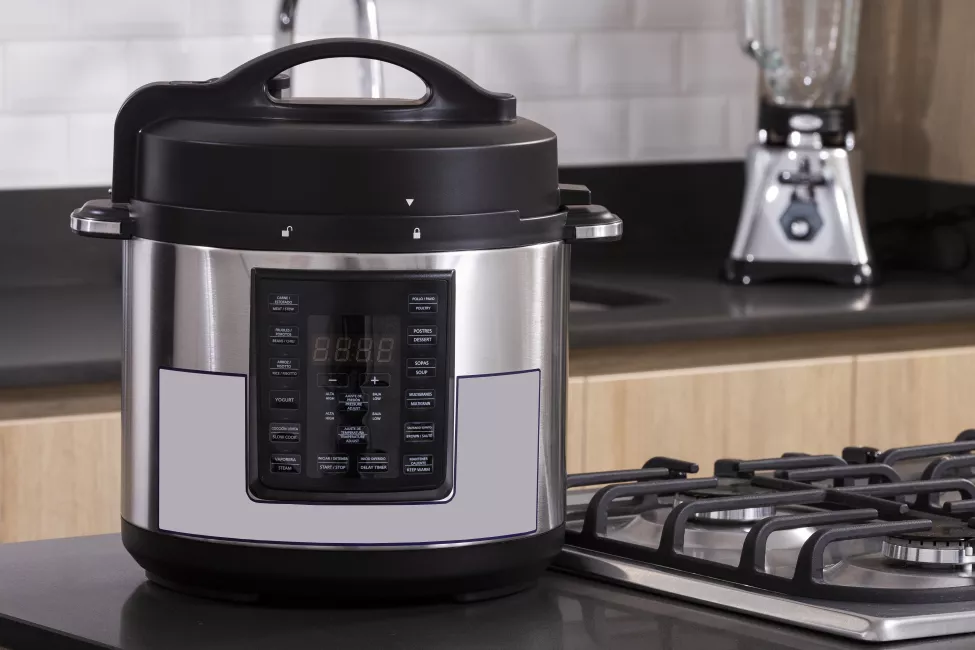
In addition to multiple components, complex multifunctional devices pose a variety of new potential hazards. For example, a modern oven may incorporate several capabilities into one device, such as a camera inside to determine whether food is done, programmable heaters and steam modes, and conventional and convection oven settings. These place additional burden on consumer products and electronics companies to anticipate all the hazards that might occur due to mechanical and design defects as well as use case scenarios.
From an engineering perspective, some of the most common types of hazards include:
- Mechanical/physical hazards, such as laceration from exposed or unsecured blades and tip-over instability of appliances, exposing hot contents or parts
- Electrical hazards, for example, improper connections, component ratings, or grounding; missing fail-safe mechanisms; damaged wire insulation; exposed electrical parts; unprotected electrical outlets; insufficient cord strain relief; water intrusion; insufficient heat dissipation; and other issues
- Thermal hazards from damage or internal defects that cause overheating or arcing leading to burns or electrical fires
Customized design and safety reviews offer value
Although a kitchen appliance may be designed following standard industry guidelines, a customized design and safety review consisting of document review and physical product testing can uncover hidden hazards, omissions in testing, or issues with critical components that could pose safety risks to users.
During physical product testing, safety is assessed through mechanical, electrical, and thermal viewpoints that reflect potential uses and foreseeable misuses that standard industry tests may not capture.
Customized testing often includes:
- Examining the layers of protection by bypassing a safety feature and testing the robustness of protection mechanisms, including redundant features that protect users in the event one safety feature fails
- Assessing the overall build quality and potential mechanical hazards including sharp edges, pinch points, finger entrapment, and tip-over instability
- Examining PCB quality through single-fault condition testing at both the PCB and full-device level
- Evaluating potential thermal hazards, such as fire or burn injury risk, by measuring the temperature of surfaces and key parts during normal operation, foreseeable misuse, and abnormal operation, such as when critical components on the PCB are short-circuited or open
In the future, the race to manufacture next-generation kitchen appliances, including Wi-Fi/Bluetooth connectivity, app-controlled settings, voice assistance, and more, is certain to involve a learning curve that may multiply design flaws, manufacturing errors, and overlooked use conditions. Consequently, the demand for customized design and safety reviews is likely to become even more critical to protecting users and safeguarding companies from the risks that more complex kitchen appliances may pose.
What Can We Help You Solve?
Exponent's multidisciplinary team of mechanical and electrical engineers and materials scientists have extensive experience in design review, testing, and risk assessment. Our customized design and safety reviews can detect potential mechanical, electrical, and thermal hazards in a kitchen appliance before it's introduced to the market to help prevent user injuries and significant financial loss.
Insights
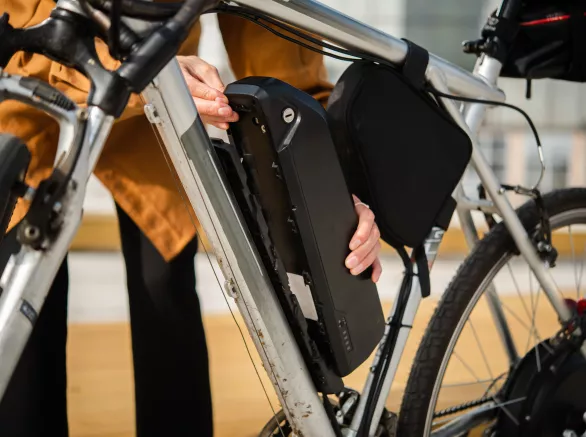