November 11, 2024
Reconsidering battery design, testing, and hazard analyses in the context of extreme weather impacts
Thermal runaway events resulting in battery fires and explosions in battery powered systems are principal among concerns for battery manufacturers and other stakeholders integrating lithium-ion (Li-ion) batteries into their products. This is especially important for systems with batteries that have higher energy storage capacities, such as those used in electric vehicles and grid-scale energy storage applications.
During the design and validation process for lithium-ion cells and batteries, environmental conditions (e.g., temperature and humidity) under which the batteries are expected to be stored and operated are critical factors in selecting sealants, adhesives, and other structural components. Severe weather conditions can accelerate the degradation of battery systems. Stressors associated with these conditions include exposure to prolonged elevated temperatures and the corrosive impact of water ingress into battery enclosures and, potentially, the cells themselves. An example of this danger occurred following the landfall of Hurricane Ian in 2022 on the Florida coast, when several EV batteries that had been submerged in saltwater burst into flames.
Battery manufacturers, integrators, and OEMs can mitigate some of these risks by carefully considering battery form factors, assembly processes, enclosures, and the geographic deployment of their fleets. To validate these design choices, they can perform hazard analyses and test batteries under conditions such as elevated temperatures, high humidity, and corrosive environments. These studies offer a thorough characterization of battery performance, help identify potential failure modes, and evaluate the effectiveness of integrated components, controls, and safety features in the context of harsh environments and severe weather events.
Harsh weather design and deployment factors for Li-ion batteries
Minimizing Li-ion risks from potential water ingress and elevated ambient temperatures means considering the following factors both individually and holistically.
Form Factor
The geometry, aspect ratio, and casing materials of Li-ion cells dictate specific design and manufacturing requirements for Li-ion battery packs — all of which can factor into considerations of weather-related battery risk.
Depending on the application, cylindrical cells may be an optimal choice relative to prismatic cells in conditions where extreme heat is a factor, due to their shape and the resulting gaps created when arranged in packs, facilitating increased heat dissipation.
Likewise, battery cell form factor plays a role in risk analysis of water ingress. While pouch cells are enclosed with an aluminum-coated plastic film preventing water penetration, cell cap, vent, or other design features in cylindrical and prismatic cell casings can create pathways for moisture intrusion if not manufactured to best practices or designed with particular end-use conditions in mind.
While EVs may impose more stringent requirements on cell selection due to mechanical factors such as vibration and collision, environmental conditions — including extreme temperatures, humidity, and exposure to contaminants — are important considerations for both EVs and grid-scale battery energy storage system (BESS) installations.
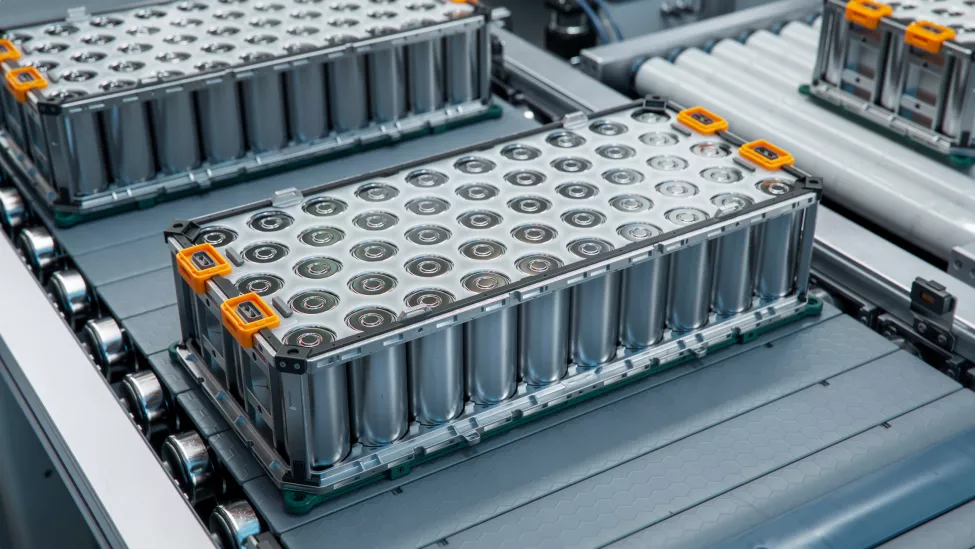
Battery Integration, Assembly & Enclosure
Battery pack assembly and enclosure are critical factors to consider in safeguarding battery cells from severe weather conditions and reducing the risk of thermal runaway. Manufacturers and utilities need to weigh the advantages and disadvantages of different types of enclosures — including material, shape, size, and placement — to select designs with site-specific environmental factors in mind. For example, enclosure geometry and enclosure materials can be selected to optimize heat transfer and pressure release and mitigate water intrusion.
In circumstances where high humidity is identified as an acute or chronic threat, specifying high ingress protection ratings can help improve battery safety, as can routine maintenance and testing of enclosures and their seals with an assortment of installation-specific water infiltration tests, particularly after potential exposure to harsh weather. Adoption of best practices regarding installation inspections is also key. Investigation into the 2022 Elkhorn fire, in Moss Landing, California — site of one of the world's largest utility-owned BESS facilities — concluded that faulty installation of a vent shield, and the subsequent dislodging of an umbrella valve, followed by "significant water ingress," precipitated electrical arcing and thermal runaway.
Geographical Deployment
The location where installation of a battery pack takes place is another consideration that can significantly influence its performance and safety. Factors to consider include whether the battery will be installed in a controlled environment or outdoors (like the recent 25 MW BESS installation on the Caribbean island of Curacao), with direct exposure to the elements, including potential flood impacts. Depending on various factors, one battery pack may be suitable for deployment in a coastal location, marked by high humidity and an accelerating increase in tropical storms, while others will not. Battery modeling, data-driven methods, and simulation analyses can be employed to evaluate strategies for mitigating the risks posed to BESS applications by environmental stressors, such as severe precipitation and flooding.
In considering location, it's additionally beneficial to carefully evaluate the operating specifications of battery cells, such as their operational temperature and humidity ranges, in the context of real-world conditions. While one cannot consider all possible environmental scenarios, especially for EVs and energy storage modules likely to travel from region to region or be installed across different locations, holistic assessments — including reliability testing of batteries at above and below recommended operating temperatures, temperature cycling, and thermal propagation assessments — can be valuable in determining optimal component selection for stationary battery install locations.
Li-ion ubiquity, age-related risk, and weather considerations
Understanding Li-ion failure mechanisms at the system, module, and cell level is essential to designing safer and more resilient battery systems, particularly in the evolving context of extreme or unprecedented weather events — a situation further complicated by the increased proliferation of home and office uninterruptible power supplies (UPS), portable power stations, and compact, portable power banks designed as reliable backup energy supplies in extreme weather-driven blackouts. The risk of potential Li-ion battery failures in EV, utility, and in-home applications is likely to increase given the growth of battery use — particularly in the energy sector, which now accounts for as much as 90% of annual Li-ion battery demand.
Additionally, the aging of so many large, energy dense Li-ion batteries must be considered, especially when they may be subjected to extended periods of elevated temperatures or high humidity. While the life expectancy of a smartphone may be just a few years, the expected use of EVs and grid storage applications could be a decade or more, with their installed batteries, safety enclosures, safety mechanisms, and other device components aging accordingly, presenting risks in terms of degradation and exposure that increase over time.
To help make their products safe and resistant to evolving climate factors, battery manufacturers can benefit from weighing the trade-offs between different form factors, cell design and hermiticity, component choices, and installation locations to design or identify battery packs that can withstand the environmental stresses presented by each location, going beyond baseline testing standards to optimize site-specific battery design in service of durability, longevity, and safety in hazardous environments.
What Can We Help You Solve?
With decades of experience working on batteries and energy storage systems, Exponent's multidisciplinary battery experts provide total product lifecycle support across chemistries and applications. Our consultants offer risk assessments, compliance and recall support, design reviews, vendor and supply chain evaluations, and bespoke testing that goes beyond the standards.

Batteries & Energy Storage
Supercharge performance, reliability, and safety across all stages of the battery and energy storage product lifecycle.
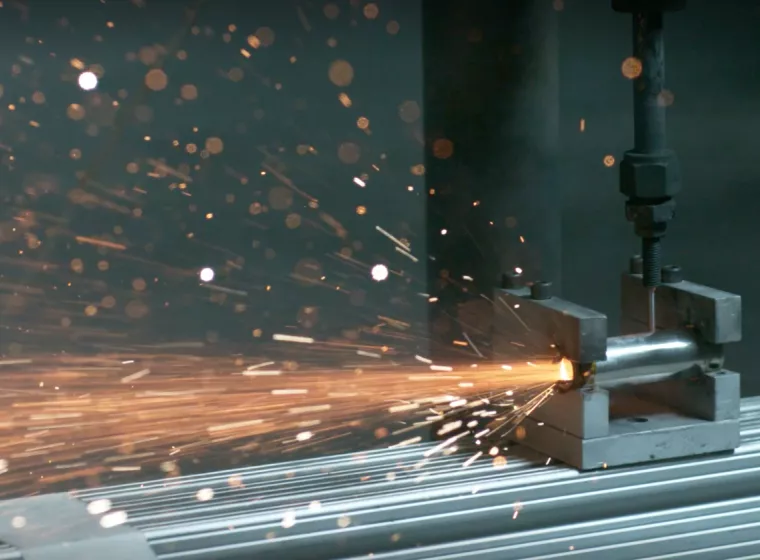
Battery Failure Analysis & Investigation
Comprehensive battery failure analysis to determine the root causes of failures and identify opportunities for mitigation.
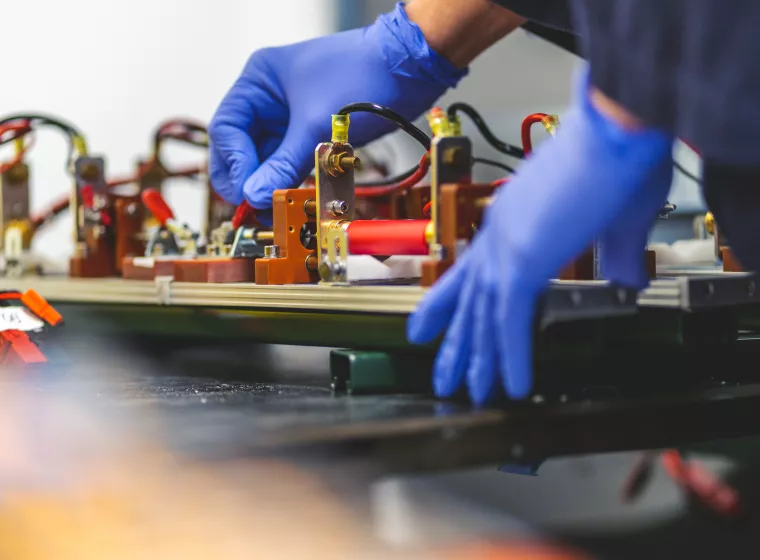
Battery Risk Assessments & Corrective Action
Li-ion battery risk assessment and corrective action services, including cost-effective tools for long-term monitoring.
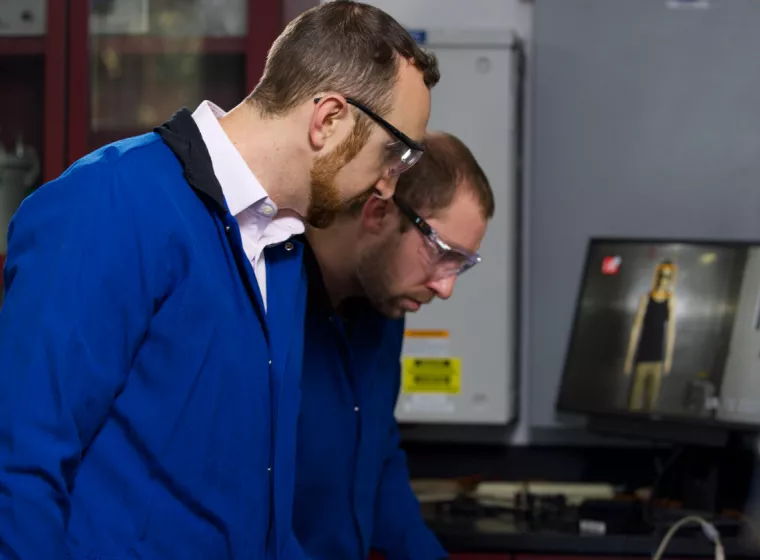
Battery Safety & Recall Support
Support for foreseeable use and misuse scenarios, industry and product requirement evaluations, and incident prevention.