August 28, 2024
Capturing innovation through risk management and engineering perspectives
Hydrogen is quickly becoming a key part of our transition to low- and zero-carbon energy. The ACES Delta, a joint venture between Chevron and Mitsubishi Power in Delta, Utah, is currently generating hydrogen with alkaline electrolyzers using surplus renewable power generated in California. The facility will use salt caverns to store up to 11,000 metric tons of hydrogen and initially blend it into natural gas, powering gas turbines at the Intermountain Power Plant in Utah. In the future, the hydrogen produced by projects like ACES Delta could be used to power long-haul trucking and shipping or even heat homes.
While hydrogen has long been promised as a high-impact solution for myriad applications, development and market maturity are reaching a momentous inflection point, generating demand for the increased research and engineering perspectives needed to address safety and risk issues so that industrial gas companies, refiners, chemical companies, and even space flight entities can realize new, innovative objectives.
Why hydrogen?
Hydrogen's key benefit is that it generates only water when reacted with oxygen to release energy. The International Energy Agency (IEA) projects demand for hydrogen to grow 6% annually to more than 150 million tons by 2030, 40% of which is associated with non-traditional uses including synthetic fuels (synfuels), power generation, and transportation.
Although hydrogen's properties make it an appealing fuel, challenges related to production, transportation, and storage have slowed its use on a large scale. For utilities, heavy industry, and transportation stakeholders who foresee using hydrogen for energy transportation and storage, evaluating sources and production methods, managing risk, and paying close attention to evolving government regulations are all crucial.
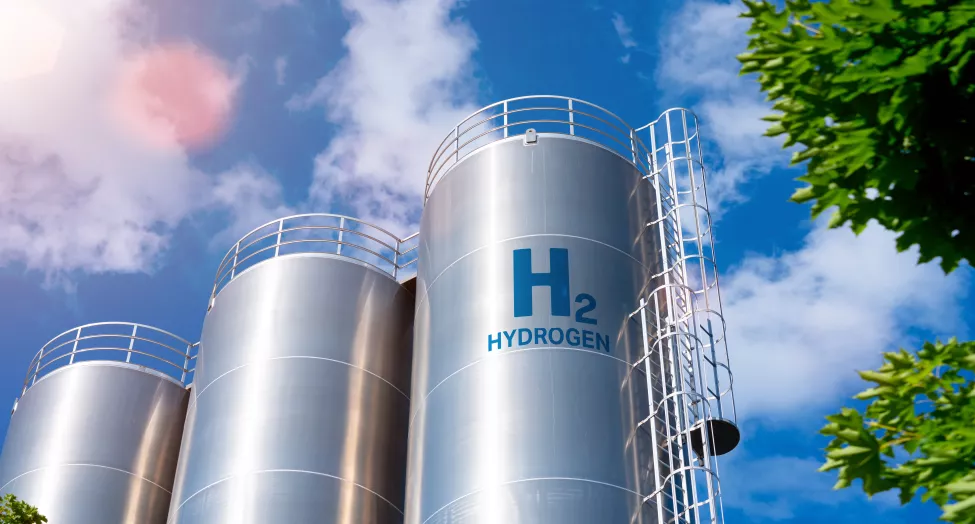
Considering hydrogen sources
Hydrogen may be the most abundant element in the universe. Most is locked in larger molecules like water, ammonia, and hydrocarbons, requiring various chemical processes to split it away from those other molecules. Most hydrogen in use today is produced from hydrocarbons through processes that release carbon dioxide. When considering hydrogen as a fuel, understanding where it comes from, and the greenhouse gas emissions associated with different production methods, is key to overall sustainability goals for industry.
"Gray hydrogen" is generated from natural gas and coal. Most hydrogen production from natural gas employs the steam methane reforming (SMR) process, where natural gas is combined with steam and catalytically converted at high temperatures to a mixture of hydrogen, carbon monoxide, and carbon dioxide. Additional hydrogen can be obtained using the water-gas shift process that reacts carbon monoxide with water to generate more hydrogen and carbon dioxide. Hydrogen is then separated from the remaining carbon monoxide and carbon dioxide.
SMR reactors are heated externally by burning fuel gases. Catalytic autothermal reformers (ATR) and non-catalytic partial oxidation (POx) processes for gray hydrogen production from hydrocarbons use oxygen to provide in situ heating in the reactor. They too generate a CO2-containing gas stream. Producing hydrogen from coal typically uses a process called gasification and has an even greater carbon footprint.
The cost of producing hydrogen from renewable electricity is expected to fall 30% by 2030, which is likely to make green hydrogen more competitive and motivate development.
For hydrogen to be a low- or zero-carbon fuel, it will need to be obtained through processes that either capture carbon dioxide or avoid producing it altogether. Hydrogen produced without carbon dioxide emissions is known as "green hydrogen," while "blue hydrogen" refers to processes that capture the carbon dioxide generated. There are three emerging methods for producing blue/green hydrogen and eliminating the associated carbon dioxide emissions from the hydrogen production process:
- Carbon capture and sequestration (CCS) — Traditional methods of hydrogen generation are used to split hydrogen from hydrocarbons. The resulting carbon dioxide will be captured at the plant, transported in pipelines, and stored underground. Carbon dioxide pipelines present their own hazards. Carbon dioxide is denser than air and is an asphyxiation hazard if released near populated areas in the event of a leak or rupture. This scenario occurred when a carbon dioxide pipeline ruptured in Satartia, Mississippi, in 2023, resulting in 200 people being evacuated and 45 hospitalized. As CCS techniques gain speed, this is a key area for risk management, requiring careful understanding of existing (and evolving) standards as well as potential threats to pipeline integrity and associated assessment and mitigation strategies.
- Electrolyzers — These devices use electricity and heat to split hydrogen from oxygen in water. There are several ways to do this, but the expense of doing so can present barriers to entry for large-scale applications. Entities seeking carbon-neutral operations will also want to use energy derived from renewable sources like solar or wind. Electrolyzers can pose a particular fire risk if the hydrogen produced is allowed to mix with oxygen generated during the process and exposed to an ignition source. Such an incident occurred at a commercial facility when corrosion led to the breakdown of the cell separators.
- Pyrolysis — Pyrolysis is the thermal decomposition of materials at high temperatures. It can be used to extract hydrogen from hydrocarbons, leaving behind carbon in forms ranging from coke to soot. Depending on the specific process, catalysts may be utilized, which need to be regenerated on a regular basis. The solid carbon produced through pyrolysis does not contribute to greenhouse gas emissions and can be used for other purposes such as pigments, reinforcing polymers, or electrodes.
The cost of hydrogen production varies significantly depending on the production method. Today, green hydrogen produced through electrolysis using renewable power in the U.S. costs between USD $4-15 per kg. Gray hydrogen produced from natural gas is priced around USD $2 per kg.
The U.S. Department of Energy's Hydrogen Shot initiative seeks to make carbon-neutral hydrogen more affordable, aiming for a cost of $1 per kilogram within a decade. The cost of producing hydrogen from renewable electricity is expected to fall 30% by 2030, which is likely to make green hydrogen more competitive and motivate development. In the near term, companies may be able to surmount cost-to-entry challenges by taking advantage of government and state incentives, like those available in the U.S. and EU.
Read more of Exponent's insights on hydrogen development in our journal article, "Industry R&D Needs in Hydrogen Safety," published in Applications in Energy and Combustion Science
Challenges of transporting and storing hydrogen
At room temperature and ambient pressure, hydrogen has a very low density and is difficult to store and transport. Hydrogen must be compressed, liquefied, or chemically bonded to other elements to be stored or transported efficiently. Each method has its advantages and risks.
- Compressed Gas — Hydrogen gas is typically compressed and stored at high pressures of 5,000-10,000 pounds per square inch (psi). This is higher than compressed natural gas tanks, which are typically capable of withstanding 3,600 psi of pressure. The existing natural gas infrastructure, including storage facilities, transmission, and distribution infrastructure, is often not engineered to hold or transport hydrogen, but some U.S. utilities are experimenting with blending hydrogen with natural gas, including PG&E, National Grid, Dominion Energy, Hawaii Gas, New Jersey Natural Gas, and SoCalGas. In each case, these utilities analyzed their pipeline systems to determine whether they were suitable for hydrogen blending. Standards for blended hydrogen-natural gas pipelines are still evolving, and many companies are still assessing their existing infrastructure for use with blended gas. When considering hydrogen blends, understanding the impact on combustion properties and the nuances of material requirements and compatibility is critical.
- Liquefied Hydrogen — Liquid hydrogen has been used as a rocket propellant in space launching systems for decades. Liquid hydrogen is also used at automotive hydrogen fueling stations. In both cases, liquid hydrogen must be stored at low temperatures (-253°C or lower). The first liquid hydrogen transport ship, Suiso Frontier, has been in service since 2022 to transport liquefied hydrogen from Australia to Japan. It uses a high-performance heat insulation system with a vacuum-insulated double-wall tank structure to limit gas boil-off. Most of the existing fleet of ocean-going LNG carriers are much larger than the Suiso Frontier and use a proven double membrane cargo containment system with polyurethane and plywood for insulation, that is effective largely due to the fact that liquefied natural gas (LNG) is considerably warmer (-160°C) than liquid hydrogen. Nonetheless, as hydrogen use grows, familiarity with the design, regulatory approvals process, and operating realities of today's LNG facilities can inform equivalent activities for hydrogen systems.
- Hydrogen Fueling — Transferring liquid or compressed hydrogen from one tank to another presents risks. Workers must perform exacting sequences of processes and procedures while relying on systems with complicated components. In a recent scenario, a standard rupture disk designed to vent hydrogen to a safe location in the event of a pressure increase was replaced with a fusible backed disk. When a rupture occurred, metal fragments damaged the relief piping, dispersing hydrogen into a loading dock area and resulting in a large explosion and death of a worker. In this case, the company reviewed and renewed safety procedures and equipment to help reduce the risks of possible explosions and fires. Personnel should understand hydrogen's unique properties so that they can design, operate, and maintain hydrogen systems safely.
- Chemical Conversion — Hydrogen can be chemically bonded to other elements to create chemicals that are easier to store and transport. The two most common chemicals are methanol and ammonia. Production, storage, and transportation methods exist for both chemicals, but specific elements must be well managed to use either as a fuel. Both can be burned and produce low carbon emissions, but ammonia in particular also produces significant nitrogen oxide (NOx) emissions, which have health, environmental, and climate implications. There is strong potential here, but more development in fuel delivery systems and adapting catalytic exhaust gas treatment systems is needed to progress either option as a viable fuel.
Adhering to safe practices, including following the guidance provided in codes and standards such as NFPA 2, ASME B31.12, CGA G5.6, and ISO/TC 197 is good practice for hydrogen safety. All equipment used in the production, transport, and storage of hydrogen should be compatible with available guidance and hydrogen requirements. Many companies are already shipping hydrogen across the country using these safety protocols. In fact, there are currently around 26 hydrogen fuel stations operating in the Los Angeles area alone. These facilities disperse hydrogen from high-pressure tanks to a fleet of consumer hydrogen fuel cell vehicles that were manufactured by Honda, Hyundai, and Toyota.
As hydrogen use increases, hydrogen regulations and laws are evolving in parallel, and organizations will want to track these developments as they unfold to reduce the risks associated with storing and transporting hydrogen.
Developing hydrogen infrastructure
To realize the promise of hydrogen as a fuel, further research and development into carbon capture and sequestration technology is needed in the short term to produce carbon-neutral hydrogen from hydrocarbons. In the longer term, the production of green hydrogen at scale will require massive scale-up in manufacturing of electrolyzers that can efficiently, reliably, and safely split hydrogen from water using renewable energy sources like solar and wind.
However, the transition to hydrogen as a fuel is not just a technological challenge; it's a societal shift that demands attention to safety at all levels, including engineering, design, fabrication and construction, operation, and maintenance. As industries from shipping and long-haul trucking to power generation, energy storage, and even aviation increasingly embrace hydrogen as a zero-carbon fuel, they must also commit to the development of the necessary human resources and training as well as research and development to mitigate and manage risks.
What Can We Help You Solve?
Exponent's multidisciplinary technical and regulatory experts help clients understand the opportunities and risks of new hydrogen applications, including the challenges facing blue and green hydrogen production; flammability and toxicity issues; carbon credit markets for low-carbon hydrogen production; and the technical implications of capturing, sequestering, or using carbon dioxide from blue hydrogen production.