August 14, 2023
To curtail combustible dust explosions, industries must shift from disbelief to vigilance
As workers stamped out syringes and vial seals on the rubber-production line at a pharmaceutical plant, a dust byproduct dispersed across the factory hall, escaping conventional cleaning. It is thought that vast amounts of airborne powdered polyethylene, an ingredient used in the rubber-forming process, were sucked into vents and redistributed as a fine powder that settled on ceiling tiles, beams, conduits, and light fixtures.
After years of undetected accumulation, as much as a ton of combustible dust — about a quarter-inch thick — had become layered mere feet above the processing line. One January afternoon, without warning, the dust dispersed into a cloud and ignited.
The explosion killed six employees and injured 38 others, including two responding firefighters. A shockwave from the explosion broke windows at a neighborhood school, while an ejection of flaming debris set fire to a patch of woods two miles away. A fireball could be seen blowing out the building's exterior siding before igniting secondary dust accumulations and transforming into an uncontrolled fire that burned for two days.
Combustible dust dangers persist across industries
This 2003 combustible dust explosion remains well known to fire and explosion investigators. The catastrophe's well-documented post-explosion investigation has become a primer for thinking through the potential ignition sources and trajectories of combustible dust.
Yet 20 years later, combustible dust across myriad industries continues to cause an average of 31 explosions per year — and more than four times that amount in fires at U.S manufacturing facilities. The result is mounting efforts by regulatory bodies and standards organizations to curb the hazards of combustible dust through increased scrutiny and individualized inspections and analyses.
Enter the National Fire Protection Association's Standard 652 (NFPA 652) mandate for all dust-producing U.S. industrial operations to complete a dust hazard analysis (DHA) by 2020 — a systematic facility evaluation intended to identify potential hazards and the steps available to mitigate them.
Earlier in 2023, the Occupational Safety and Health Administration (OSHA) announced a Revised Combustible Dust National Emphasis Program that "sets forth a new approach for locating and inspecting subject establishments" based on enforcement history, combustible dust reports, and high-risk industry sectors, such as printer ink producers, commercial bakeries, and leather finishers, among others.
Although explosions have yet to see a downturn, most manufacturers now have critical information, action lists, and rationales that can help them dramatically improve equipment operations, protection, and maintenance. However, as many plant owners/operators have come to realize, DHAs often lack prioritizations for addressing unresolved hazards, guidance on potential mitigation systems, or standards for evaluating the vendors that provide them.
A detailed post-DHA roadmap can help manufacturers safeguard their facilities against combustible dust while not losing sight of the big picture: Many finely divided solids can become dangerous dust that, once suspended in air at certain concentrations, can result in ignition and explosion.
Since most companies cannot solely rely on in-house dust hazard specialists, manufacturers must simultaneously learn about equipment to safeguard dust (collection systems, flameless vents, filter receivers, etc.) while absorbing the underlying principles of combustible dust to evaluate new and ongoing hazards, specific solutions, and understand "the why" behind product recommendations.
The ongoing industrial hygiene of daily dust removal mostly falls on a manufacturing workforce that both OSHA and NFPA have recognized are sometimes inadequately trained on the dangers of combustible dust. Both agencies have advocated that dust hazards need to be better explained to frontline industrial workers.
Finding combustible dust where it develops
Following a combustible dust explosion, investigations reveal a common pattern: A manufacturer overlooked the operational risk of combustible dust and missed hazards while nonetheless meeting some minimum compliance standards. Even once post-incident evaluations identify dust as the culprit, many plant owners/operators and manufacturers remain in disbelief that such fine powders and dust byproducts pose damaging explosion risks.
Exponent has performed numerous DHAs using our Combustible Dust Testing Laboratory, where depending on the depth of testing required, our methods include performing powder explosions under contained conditions for safe viewing. Although a DHA may fall short of a complete risk-reduction roadmap for manufacturers, it has the potential to reveal the real and imminent danger that combustible dust can pose.
Managing the risks of combustible dust means identifying and isolating the airborne pathways of manufacturing dust and particulates and evaluating dust hazards in processes and equipment — while also training your workforce in dust hazards.
The ongoing industrial hygiene of daily dust removal mostly falls on a manufacturing workforce that both OSHA and NFPA have recognized are sometimes inadequately trained on the dangers of combustible dust. Both agencies have advocated that dust hazards need to be better explained to frontline industrial workers.
As such, manufacturers can unlock action from a DHA by grasping information that quantifies the size, severity, speed, and likelihood of a dust cloud reaching explosible conditions — based on possible concentrations of particulate matter and oxygen — and finding a competent ignition source to identify initial approaches for mitigating hazards.
Explore Exponent's Combustible Testing Laboratory
The dust hazard analysis is done, now what?
After completing a DHA, facility operators commonly find themselves with a list of recommendations for addressing potential noncompliance issues. In many instances, however, DHA teams rely on prescriptive guidance from consensus standards in their analysis, thus focusing on prescriptive requirements as the simplest way to resolve those issues. This approach can come up short in evaluating the feasibility of implementing strict prescriptive requirements, which often falls outside the scope of the DHA.
For example, a DHA may recommend that explosion protection such as deflagration venting or explosion suppression be retrofitted onto existing equipment. However, implementation may be infeasible depending on the original process design or facility layout. In these types of circumstances, facilities look for additional guidance on how to further characterize and manage their combustible dust hazards.
Additionally, addressing the recommendations of a DHA may involve extensive capital planning and scheduling that are also not part of its analysis. As a result, facilities can be left with multiple challenges: How should you address potential noncompliance when adopting the prescriptive requirement is infeasible? What recommendations or action items should you address first? Where will the greatest risk reduction be realized based on your allocation of resources?
This is where Exponent's combustible dust experts provide real value. Consensus standards often offer an alternative means of demonstrating compliance beyond the adoption of prescriptive requirements. However, these alternatives require more detailed expertise and the ability to demonstrate an acceptable equivalency of either performance-based or risk-based analysis compared to the adoption of the prescriptive requirements. Exponent's combustible dust experts can help a facility operator evaluate the options to address the issues identified by the DHA team, understand the underlying risks, and gather the insights necessary to select appropriate solutions for implementation.
In the example above, additional testing could reveal important details about the minimum ignition energies of materials handled or the specific layout of the work areas. Given this additional information, the facility operator could consider interim mitigation of the combustible dust hazard by focusing on ignition source control and adopting administrative controls, including limiting worker occupancy in the areas surrounding the equipment when in operation.
Examples of challenges that may result from a DHA's list of recommendations and how to create an actionable plan vary based on the actual circumstances but may include:
- Prioritizing recommendations based on the risks posed to equipment, personnel, and business continuity
- Streamlining sampling and testing programs to maximize efficiency for clients who handle a wide variety of materials that present unique dust hazards
- Navigating changing requirements as industry-specific standards are consolidated, while understanding the historical context of prior revisions
- Evaluating mitigation options including prescriptive guidance in standards, performance-based equivalency, or risk-based approaches
- Leveraging knowledge of new emerging technologies for mitigating combustible dust risks
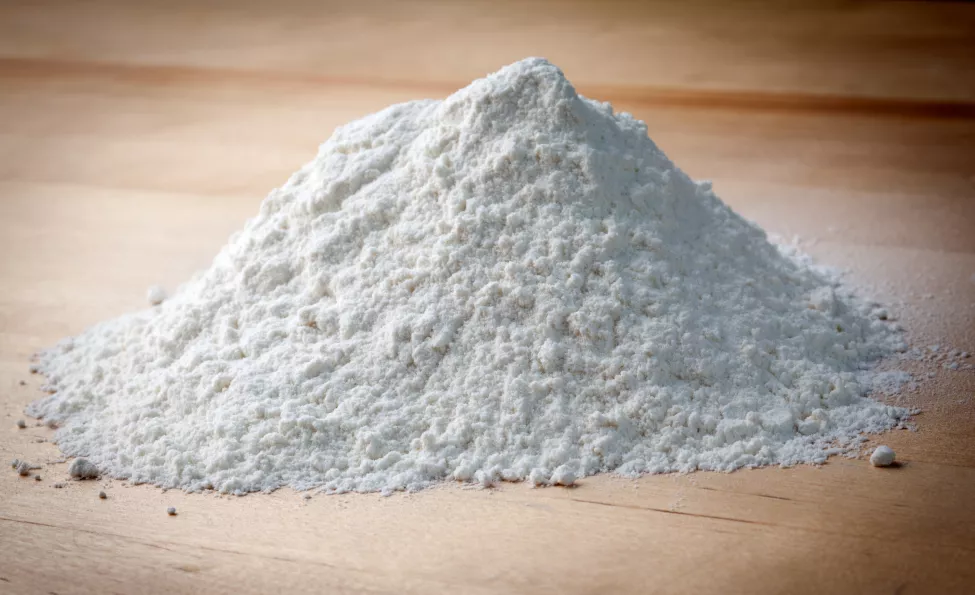
What's next for addressing dust hazards?
Although NFPA is a nonprofit safety organization, their codes are commonly adopted, incorporated, and cross-referenced in international building and fire codes, and federal and state governments recognize their standards as generally accepted good practices. Historically, NFPA's combustible dust standards have been commodity-specific, with dedicated standards for industries such as agriculture, woodworking, metals, etc. In a move that would streamline combustible dust safety practices, NFPA is now seeking public and manufacturer input for the long-awaited 2025 release of NFPA 660, a "one-stop" standard that should consolidate six different existing industry standards for safeguarding and removing combustible dust.
This forthcoming streamlining of standards, coupled with an uptick in federal enforcement action, means that a record number of U.S. companies could be in a renewed position to protect their facilities against dust, but they will need support with the application of new or unfamiliar requirements. Facilities that know their dust hazards well will always be in a good starting place.
Don't let the combustible dust settle
Fugitive dust that settles outside of equipment can become dispersed during the early stages of a combustible dust incident and result in violent, damaging, secondary explosions. Even small quantities of fugitive dust can pose a problem. Most standards recommend dust be cleaned if the layer on the ground is thicker than 1/32-inch to 1/8-inch (i.e., approximately half to twice the thickness of a penny) and covering more than 5% of the work area.
Achieving a safe workplace environment under that threshold remains an ongoing challenge for companies that must quickly grasp the risks at hand while moving to implement processes to contain, isolate, and remove combustible dust. Deciding between essential and non-essential fugitive dust removal requires custom data on how a facility produces and disperses dust.
Similarly, as industrial processes become more integrated and efficient, the risks associated with interconnected equipment can become more acute. Explosions can become more severe as they propagate through ductwork and into other equipment, and requirements to evaluate and address these dust hazards are also becoming more prescriptive.
Devising and maintaining effective control and mitigation strategies requires a high-level of expertise, as the level of risk can vary from process to process and day to day, as new dust hazards may result from events such as the launch of new processes, lapses in cleanliness, or changes in raw materials. Understanding and managing your dust hazards — and reducing persistent annual dust explosions — continues to be a critical priority.
What Can We Help You Solve?
Exponent's fire and explosion experts leverage our combustible dust testing laboratory to help clients develop effective dust hazard mitigation strategies. We help you select from a variety of standard ASTM International tests, such as combustibility and explosibility screenings, and customized methods for accident recreation, hazard demonstrations, and hazard assessments. Several Exponent scientists sit on or chair NFPA dust standard committees.