October 29, 2024
Four key challenges facing battery manufacturers as evolving requirements for the use — and reuse — of finite resources take shape around the world
The boom in battery demand — for EVs, grid energy storage applications, and consumer electronics — has raised concerns over the scale of the industry's dependence on critical materials in finite supply, such as lithium, cobalt, graphite, copper, and nickel, as well as the widespread environmental implications of their mining, refining, and disposal.
To combat these concerns, European and U.S. state and federal regulators will soon provide guidance on digital tracking and material circularity programs for the critical minerals essential to the battery chemistries of today and tomorrow. These efforts, although different in scope and detail, all aim at enforcing transparency in carbon accounting among OEMs, battery makers, and product manufacturers and, ultimately, improving stewardship of precious resources across their total product lifecycle (see fig. 1), which may now be recovered through dismantling batteries at their end of life and extracting minerals for reuse in new applications.
These regulations are poised to fundamentally change responsibilities for industry stakeholders now facing unprecedented demands for extensive data collection, validation, and exchange, along with new compliance challenges regarding the recycling and reuse of batteries and battery components.
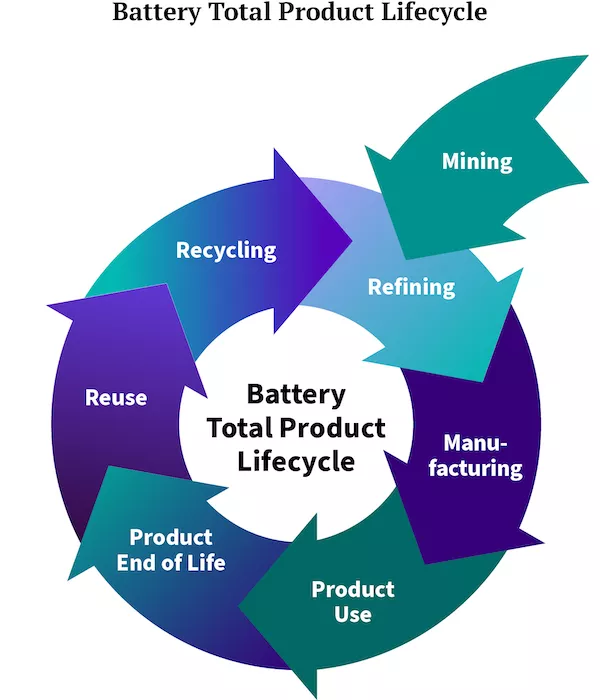
The TRACE Act and Battery Passport
The Critical Material Transparency and Reporting in Advanced Clean Energy (TRACE) Act, or H.R.8187, was introduced in Congress in April 2024 amid global momentum for supply chain tracking, digital record systems, and material recycling initiatives for batteries. The previous year, the Global Battery Alliance launched its battery passport pilot, featuring a digital document of a battery's complete lifecycle. Soon after, the EU's Battery Passport program, set to take effect Feb. 1, 2027, was formalized through the EU Battery Regulation Amendment.
The TRACE Act gives the secretary of energy one year to start a digital identification program to increase supply chain transparency for critical minerals employed in batteries above 2 kWh, including in EVs and grid storage systems. If signed into law, it would recommend collecting and sharing information about batteries, including their composition and chemistry, materials sourcing, carbon footprints, recycled content, and levels of materials recovery, as well as associated, mining-related human rights issues.
At their core, the TRACE Act and the EU Battery Regulation Amendment seek the sweeping digitalization and standardization of information about the raw materials in battery supply chains. Yet these programs will do more than facilitate the creation of globally accessible digital twins of commercial batteries. The EU policy (with a broader scope than TRACE that could provide a model for future domestic legislation) and eventual adoption of exacting, progressive carbon footprint thresholds and mineral recovery rates have the potential to reshape how lithium, graphite, and other critical minerals are sourced and processed for use in utility-scale energy storage, EVs, and e-mobility devices.
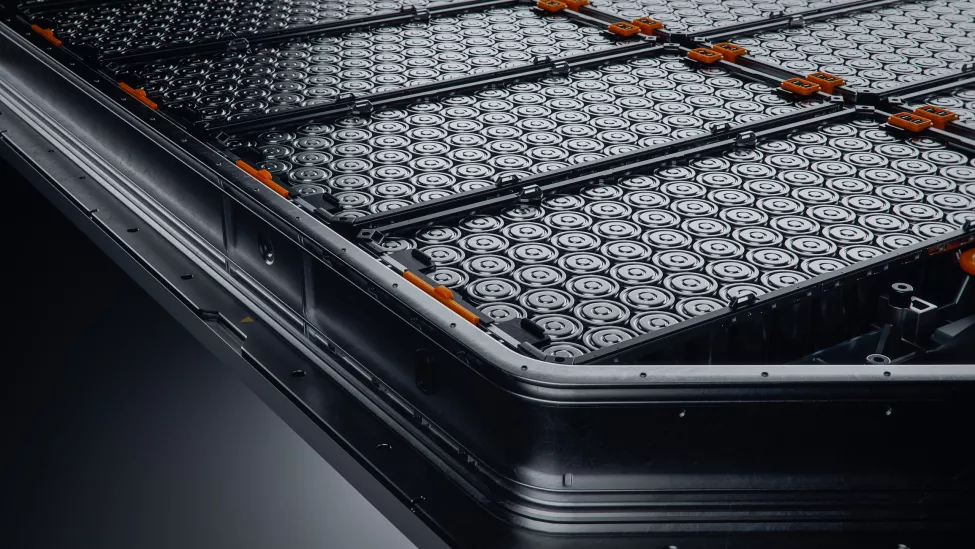
Four key mineral compliance challenges
As these emerging regulations take shape, battery industry stakeholders will benefit from investigating and understanding their compliance responsibilities, information dependencies, vulnerabilities, and risks, as well as the types and sources of materials used in their products at a more detailed level than ever before. Key challenges facing industry stakeholders include the following.
1. Accurately interpreting global critical mineral regulations
Beyond TRACE and the EU Battery Passport, multiple additional initiatives for tracing critical minerals and documenting the full circularity of battery components are in development around the world, carrying significant implications for global organizations. Examples include the German Supply Chain Act, Europe's Proposal for Ecodesign for Sustainable Products Regulation (ESPR), California Assembly Bills 2832 and 2440, and California Senate Bills 1215 and 615 (the latter is currently being drafted) — all reflecting a variety of provisions, some overlapping and some distinct.
To manage these regulations, it is crucial for OEMs, mining operations, and EV and grid storage manufacturers — as well as auto dealers, repair shops, and battery testing and recycling organizations — to develop an exacting understanding of their emergent responsibilities relative to upstream business partners and end-of-life and secondary market stakeholders.
It's likely that reporting on mineral recovery rates (typically, the percentage of a mineral harvested compared to the volume of original ore) and the recycled contents of critical minerals (how they are extracted from initial product applications and repurposed for secondary uses) is likely to present new, unfamiliar obstacles. These issues will be compounded by differing timelines and how specific regulatory frameworks may diverge or align.
As a starting point, organizations that begin gathering details and identifying gaps between proposed regulations and their current practices will be best positioned to adjust according to key deadlines. Conducting a thorough regulatory review can start with questions such as:
- What data must be disclosed and to whom?
- What information should partners provide up and down the value chain?
- What are the specific timelines for information disclosure and other criteria, including compliance with carbon footprint thresholds?
- What information doesn't require disclosure?
- How should organizations ensure sensitive and proprietary enterprise data, such as trade secrets, be kept private and secure?
2. Upstream data resourcing and validation
For battery OEMs — or other entities recognized by regulatory bodies as the responsible economic operator or equivalent — obtaining reliable critical mineral data from business partners will be paramount. However, cell and battery manufacturers, vehicle and grid storage manufacturers, and battery recyclers must first rely on data supplied by the parties that source and process a battery's raw materials — principally, mining operations. This will require OEMs and other downstream stakeholders to take a new view of upstream sampling, calculation practices, and data validation methods.
Processes used to purify and refine lithium, nickel, and other minerals essential to battery production vary widely with vastly different carbon footprints. Geographic location is likewise a factor, as processes such as nickel smelting from low-grade ore and the Acheson process used to produce graphite are particularly carbon-intensive and, when employed in countries like China, usually reflect a coal-heavy energy mix.
Calculating the carbon footprint for sourcing and refining critical minerals is a complex undertaking, involving determinations of energy use in diesel combustion vehicles, heating and cooling production processes, and additional indirect factors. Data gaps at this initial stage of the total product lifecycle can compromise upstream calculations, significantly impacting OEMs and other partners downstream who may ultimately be held responsible by regulators.
Given ongoing human rights abuses related to the mining of critical minerals in the Democratic Republic of the Congo and elsewhere, stakeholders will benefit from independent evaluations and audits of battery mineral sourcing to support alignment with ethical and sustainable supply chain best practices and brand stewardship.
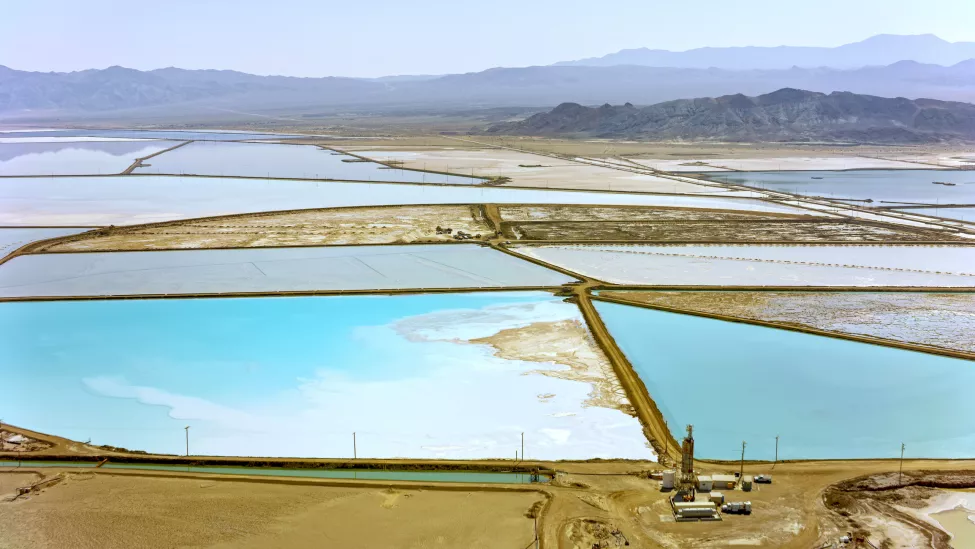
3. Strong data governance across the value chain
Given these evolving, rigorous demands for industry, new data governance processes will likely be necessary for many organizations. Battery industry stakeholders will need access to cutting-edge data tools and techniques that support the objective evaluation of complex economic networks.
These programs will require sharing data with supply chain partners, from precursor cathode active material (pCAM) producers to re-manufacturers, dismantlers, and the general public, each with appropriate access permissions. Machine-readability, system interoperability, and data flexibility will be key. Data flexibility is essential to allow structured data to adapt as a battery's attributes change across its lifecycle, including in reuse and recycling scenarios, where, for instance, raw metals may be shredded, melted, dissolved, reprocessed, and apportioned into new batteries, applications, industries, and geographies — restarting the lifecycle of the battery and its reporting responsibilities over again.
Additional data governance challenges include the structure and presentation of instructions for dismantling, recycling, or disposing of a battery and its raw materials. Optimal guidance and hazard warnings that serve different audiences, including consumers, will also fall to the responsible economic operator. Taken together, meeting these new demands can be accomplished through sophisticated resource planning and manufacturing data governance processes, integrations, and evaluations.
4. Aligning materials processing with best practices
The EU Battery Regulation Amendment stipulates maximum, full lifecycle carbon footprint thresholds (by 2028), specific critical mineral recovery rates to be met through battery recycling, and percentages of recycled minerals that must be incorporated into new batteries — escalating from 6% and 16% for lithium and cobalt, respectively, by 2031, to 12% and 26% by 2036.
However, according to market analyst Benchmark Mineral Intelligence, without significant build-outs of recycling capacity and improvements in mineral recovery rates, European recovery and recycling operations will fall short of the lithium and cobalt thresholds established by EU regulations.
Even as U.S. initiatives are under way to accelerate development of domestic mines for critical minerals and reduce reliance on conflict mineral quarries and those with unsustainable emissions practices, many obstacles stand in the way of that goal, including poor ore quality, geological complexities, regional regulatory nomenclature and standardization issues, and a shortage of skilled domestic workers. As with the EU, U.S. domestic efforts to create more critical mineral circularity — and establish attainable benchmarks in line with the EU's program — will hinge on ramping up domestic mineral recycling capacity and quickening the pace of innovation in hydrometallurgical recovery technology.
To prepare for compliance in the meantime, OEMs and other industry stakeholders can begin with:
- Rigorous supply chain mapping and analyses
- Mining and refining partner evaluations
- Adoption of cutting-edge battery production and mineral recovery and recycling processes
Staying competitive in this rapidly changing commercial landscape will mean embracing carbon accounting and critical minerals transparency and circularity
Battery market compliance horizons
With recent escalations in R&D investment fueling the commercialization of new battery technologies for EVs and grid energy storage, including solid state, silicone anode, and sodium ion chemistries, OEMs and their supply chain partners will soon be navigating a market — and regulatory environment — that is progressing rapidly toward greater accountability across the entirety of the total battery product lifecycle.
Staying competitive in this rapidly changing commercial landscape will mean embracing carbon accounting and critical minerals transparency and circularity as both environmental imperatives and market opportunities — for batteries above 2 kWh, but also for smaller consumer electronics and medical devices, for which similar battery regulations may follow. In a post-battery passport economy, stakeholders leading the transition toward a sustainable value chain will be those who prepare now for the industry's expanding compliance requirements.
What Can We Help You Solve?
Exponent leverages decades of experience in vendor and supply chain evaluations and mapping, regulatory compliance support, battery chemistry consulting, battery design reviews, and risk and safety assessments for utility-scale energy storage systems, EVs, and more. Our multidisciplinary batteries consultants offer total product lifetime support for all battery chemistries.