July 30, 2024
Devastating fires in high-rise buildings worldwide highlight critical safety and compliance gaps, underscoring the value of advanced modeling
High-rise façade fires are a global concern, having more than tripled between 2004 and 2018. In 2017, the 24-story Grenfell Tower in London fire captured international attention when it burned for 60 hours and killed 72 people — resulting in industry-wide scrutiny and reevaluation of the fire spread risk of façades and associated international standards.
Despite heightened awareness of their danger, by 2021 devastating façade fires in high-rise buildings were occurring at a rate of more than once per month worldwide. More recent incidents include a luxury residential complex fire in Valencia, Spain, leading to 10 fatalities, and a fast-spreading, multi-story fire at an apartment building under construction in Tver, Russia.
Combustible materials are used in building façades to improve energy performance and allow for aesthetic design flexibility. Some of the most commonly used façade types are exterior insulation finishing systems (EIFS) and aluminum composite materials (ACM). EIFS consist of a layer of insulation, reinforcing mesh, and a thin coating of exterior material. ACM systems consist of two thin aluminum sheets with an insulation material sandwiched between. Insulation can be combustible (e.g., polystyrene, polyurethane, polyethylene and polyisocyanurate) or non-combustible (e.g., stone wool, glass wool, foam glass).
Several factors contribute to the dangers of high-rise fires, including the use of combustible materials, weather barriers, and design and assembly elements that can increase fire propagation. Critically, standards around the world reflect a wide range of approaches and testing strategies, resulting in key gaps in existing regulations to address real-world fire conditions.
To resolve these challenges, materials manufacturers, construction companies, building owners, project investors, and insurers can benefit from assessing how individual materials and components pose risks to full façade systems, how full assemblies work together under different conditions, and the differences between standards that may expose buildings to critical safety gaps.
This includes understanding the limitations of testing approaches and how requirements have evolved over time. In some cases, the scope of safety evaluations needed for compliance has been reduced and may be worth reconsidering in the context of ongoing incidents. Advanced analysis and modeling tools — including FEM simulations coupled with CFD analysis, cone calorimeter testing, and thermogravimetric analysis (TGA) — can produce the in-depth insights needed to help prevent future incidents around the world.
Modern insulation, more risk?
Façade construction has evolved significantly over time, underscoring new questions about the relationship between modern building materials and high-profile fires. Traditional materials, including brick, concrete, and stone, are being replaced by ACM, fiber-reinforced polymer panels, high-pressure laminates, and cementitious base coats, which envelop the insulation needed for thermal regulation and sound attenuation.
Insulation products, combustible to varying degrees and often made from inexpensive, durable, and easy-to-install polymer materials, are being closely examined. These new materials, labeled as "combustible" or "limited combustible," are assembled with fairly complex modern façade construction details and create considerable challenges for determining fire safety using current standards and codes for testing. While "non-combustible" cladding insulation composed of wool and mineral fibers is available, it is still not as widespread as the combustible and limited combustible varieties, mainly due to its cost.
A frequent oversight when assessing fire safety of façade assemblies is thinking that the insulation choice alone will prevent a fast-spreading fire. In fact, this is only one element of a façade assembly — and while it's important, several factors contribute to risk.
Assembly and construction: Modern façade assemblies have complex construction details that can facilitate fire propagation. There is a wide variation among brands, panel types, and installation methods, including the ubiquitous cassette and wet systems — each offering their own merits and drawbacks. These façade systems include fasteners (rivets, anchors, clamps, and other devices), which can deform during fire exposure, compromise the structural integrity, and create gaps to facilitate fire propagation.
Design elements: Façade design elements unrelated to combustible insulation, AWBs, or coatings (adhesives, paints, and sealants) can contribute to fire propagation. Ventilated façades, for instance, designed with air gaps behind the cladding for added energy efficiency, can, without well-designed cavity barriers, dramatically accelerate fire spread. According to investigators, this is likely what occurred at Grenfell, where ventilated façades are thought to have created a "chimney effect," promoting the vertical fire spread that rapidly engulfed the building. Similarly, insulation used in the EIFS reportedly contributed to the high-profile 2008 Las Vegas Monte Carlo hotel-casino fire, which resulted in large-scale evacuation and millions of dollars in damage.
Limitations, conflicts, and gaps in regulatory frameworks
With heightened attention on high-rise façade fires, regulatory reform is anticipated in the coming years. In the meantime, it's critical for stakeholders to remember that even some "compliant" buildings experience rapid external fire spread due to component, assembly, and design factors that may or may not be explicitly covered by the wide variety of fire safety standards and testing strategies employed throughout the world. Currently, there is no global consensus on fire safety standards for high-rise façades.
In the U.S., NFPA 285 is the recognized assessment standard, first published by the National Fire Protection Association in 1998 and required for International Building Code (IBC) compliance. NFPA 285 covers the construction of exterior building walls of any height by evaluating the flame propagation characteristics of exterior wall assemblies containing combustible components.
In contrast, ASTM E119 — a standard test method used to evaluate the fire-resistance of building assemblies, including walls, floors, and roofs — measures the amount of time building elements can withstand exposure to fire while preventing the passage of flames and hot gases to the unexposed side of the building and maintaining its structural integrity.
NFPA 285 and ASTM E119 are two approaches that represent fundamentally different aspects of façade fire safety: whether an exterior wall (and thus, its façade assembly) promotes the spread of fire and, on the other hand, how long those elements can withstand exposure to fire without losing structural integrity. Of course, assessing fire resistance through structural assembly and fire spread are interconnected, but a building wall that is assembled to prevent fire propagation may not hold up against fire resistance tests. Likewise, components that are resistive to fire could be part of installation systems that propagate fire quickly once they fail or lose integrity under fire exposure. In short, modern façade assemblies might be required to satisfy a combination of fire propagation and fire resistance tests to pass fire safety standards, ensuring that both the materials and their installation methods mitigate fire spread and maintain structural integrity under fire conditions.
Additionally, some U.S. states and other jurisdictions use standards like NFPA 285 as the basis for their own bespoke codes rather than adopting NFPA guidance in full, resulting in exemptions and localized permitting of some non-NFPA 285 combustible cladding for use in construction. Standards are different for the use of combustible materials at different building heights as well, meaning shorter buildings may not have to meet the same level of compliance.
International regulations follow suit. Standards such as BS 8414-1 in the UK, ULC S134 in Canada, SP Fire 105 in Sweden, DIN 4102-1 in Germany, and EN 13823 (CEN, 2014) in the EU all vary in their approach to materials assessments and testing. Germany, for instance, places greater emphasis on the smoldering combustion of façade panels, while the EU's compliance test primarily assesses smoke production, heat release, and dripping from the façade or testing materials.
Reconsidering past generations of standards
Regardless of these differences, the dispersion and occurrence of large-scale façade fires raises questions as to whether any existing standard is enough. Recent research studies have shown, for instance, that peak heat flux values near window openings can be substantially larger and last longer than what is expected by NFPA 285, underscoring the importance of incorporating additional test procedures, including UBC 26-4 (the predecessor to NFPA 285) and ASTM E119, to better assess real-world façade assembly performance.
UBC 26-4 by the Uniform Building Code (since replaced by IBC) required two-story outdoor mockups of wall assemblies subjected to flames and heat flux from a simulated wooden crib fire, which produced ASTM E119 time-temperature fire exposure for one hour. UBC 26-4 was eventually replaced by UBC 26-9 — an indoor test of a single-story wall system. It's this test, where an exterior wall is subjected to flames with a predefined heat flux level from gas burners for 30 minutes, that ultimately formed the basis for today's NFPA 285, in contrast to the larger-scale test.
Rethinking standards, advancing fire safety evaluations
To assess the performance of individual façade systems and their installation components during the design phase, particularly those that have not yet been tested in the lab, cutting-edge modeling can help stakeholders bridge critical gaps between standards — both current and legacy — real-world performance, and the variety of factors that contribute to the ignition, combustion, and propagation of façade fires. These analytical and modeling tools can efficiently enable a broad assessment of potential fire conditions while also promoting compliance with NFPA 285 and other standards around the world.
Rigorous numerical analysis methods like finite element models, analytical tools including TGA, cone calorimeter tests (to measure heat release rate and smoke production of assembly materials), and radiant panel tests (to measure the propensity of materials to ignite when exposed to radiant heat), along with full-scale façade fire tests (to evaluate the performance of structural assemblies), represent opportunities for stakeholders to gain enhanced insights into the fire and smoke safety of their products and, when applied to the manufacture and installation of façade systems, additional strategies to improve building safety. To this end, façade manufacturers and construction stakeholders can benefit from looking beyond individual regulatory standards to exploring multiple angles to reduce the incidence and impacts of high-rise façade fires.
What Can We Help You Solve?
Exponent's multidisciplinary materials and thermal sciences experts use advanced modeling and assessment tools, including developing custom fire test procedures, to help clients meet NFPA 285 and other international fire safety standards. We conduct rigorous analyses in our state-of-the-art facilities to help construction stakeholders develop strategies to mitigate future fire risks.
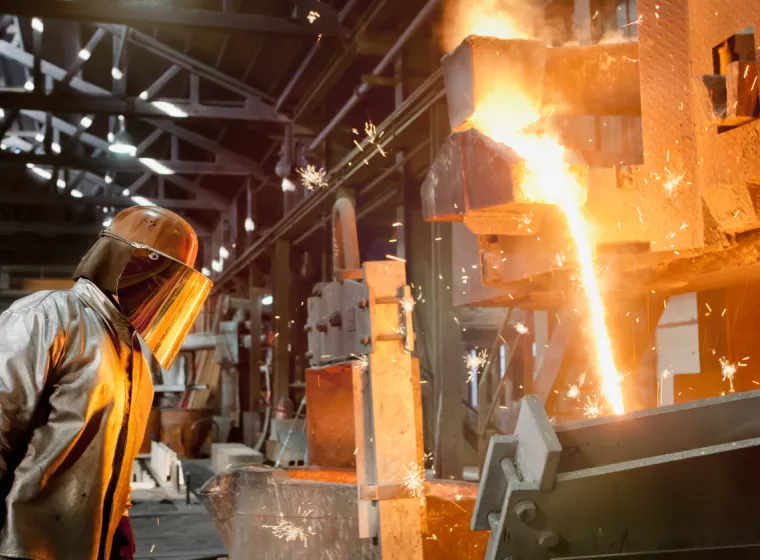
Fire & Flammability Testing
Thorough fire and flammability testing for sprinklers, smoke, and heat detectors, vehicle fire testing, and more.
![Computational Modeling [TS]](/sites/default/files/styles/cards_home_card/public/media/images/GettyImages-182174791.jpg.webp?itok=kmskqW9J)
Computational Modeling; Thermal Sciences
A less expensive and faster alternative to thermal or flow experiments.
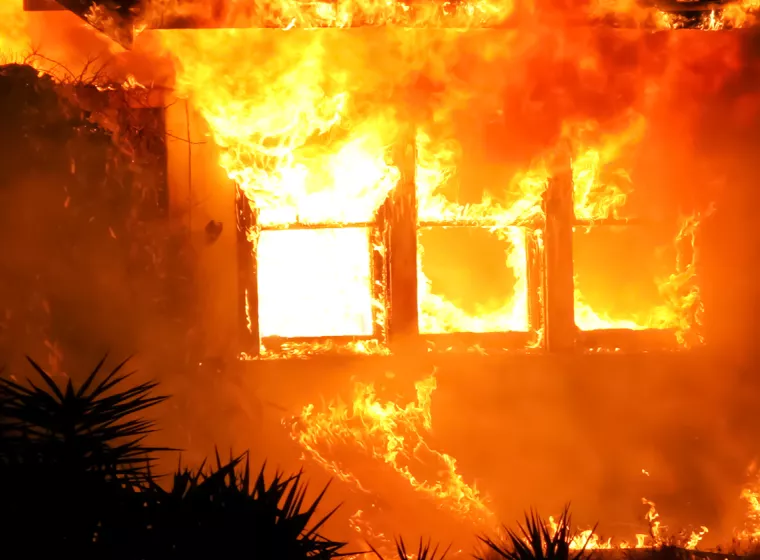
Fire & Explosion Investigations
In-depth field examinations and high-tech modeling and testing to determine the origin and cause of fires, gas explosions, dust explosions, and other explosions...
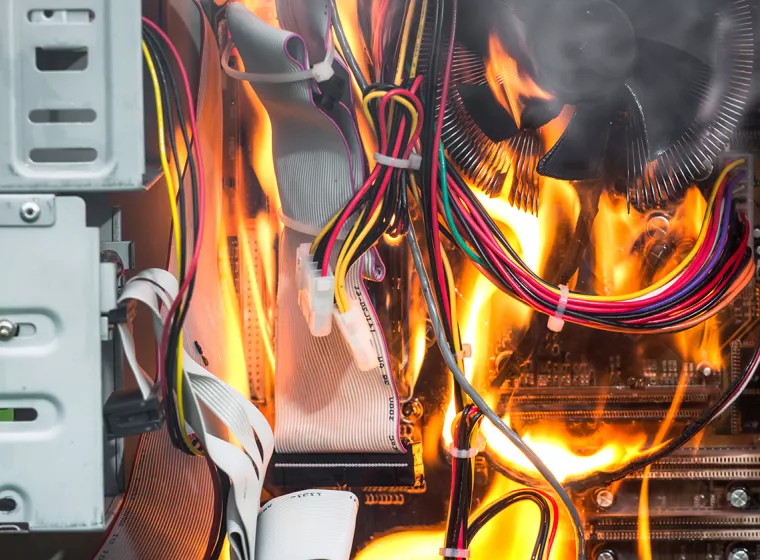
Thermal Sciences Expertise for Disputes
Evidence-based scientific insights and expert witness support for industrial fires and explosions, oil and chemical spills, and equipment failures.