May 7, 2024
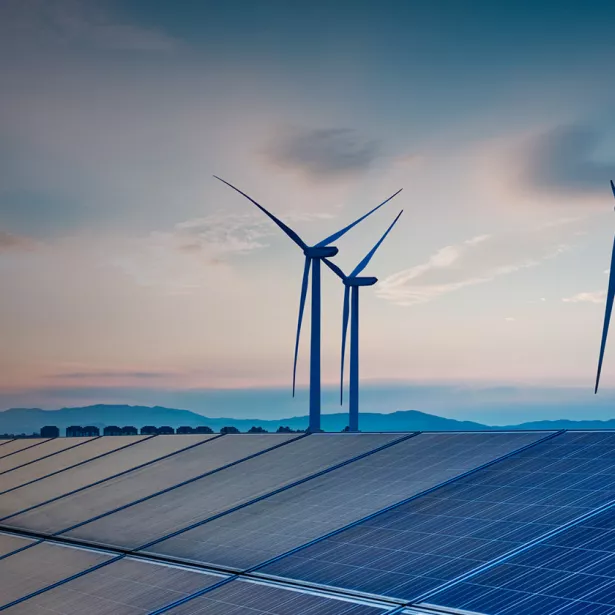
The changing pipeline integrity landscape, understanding dents as potential threats, and complying with new PHMSA requirements
According to the Pipeline and Hazardous Materials Safety Administration (PHMSA), pipeline incidents have cost the U.S. approximately $11 billion over the past 20 years. Many of those incidents were related to pipeline failures, leaks, and the resulting cleanups and repairs.
To combat these incidents while considering safety and economic implications, PHMSA published new code requirements in August 2022 affecting the way pipeline operators can respond to dents and other mechanical integrity threats (49 CFR 192.712(c)) that may increase the risk of pipeline failure. Enforcement of the new code went into effect February 2024, meaning that today, companies must be ready to perform engineering critical assessments (ECAs) to better understand the potential integrity implications of dents and other damage that "could result in a stress riser or other integrity impact."
Performing ECAs and deciding what to do with the findings pose complex challenges, raising several new questions for pipeline operators:
- What dent or damage characteristic creates a stress riser and to what degree?
- If damage or a dent is present, how can it affect the overall integrity of the pipeline?
- Are repairs or replacement warranted for the damaged pipeline?
- When should the pipeline be reassessed to maintain integrity?
The responses to these questions allow for effective ECA implementation and will be key to determining the path forward for integrity management programs, whether that means mitigation actions such as recoating, clock-spring installation, pipe replacement, or others.
Unlike strength testing or in-line inspection, an ECA provides operators with a targeted, adaptable approach for assessing and prioritizing potential integrity threats. The combination of ECA analysis with physical mitigation measures, as needed, can give operators the confidence to continue operating safely and comply with new PHMSA regulations.
Pipeline operators must identify conditions that require ECAs and submit a formalized process and procedure to PHMSA ahead of time.
Preparing for a successful ECA
As part of CFR 192.712(c)(11), "An operator using an engineering critical assessment procedure, other technologies, or techniques to comply with paragraph (c) of this section must submit advance notification to PHMSA, with the relevant procedures, in accordance with §192.18."
Given this new requirement, pipeline operators must identify conditions that require ECAs and submit a formalized process and procedure to PHMSA ahead of time.
These procedures will require a systematic approach to triage findings, evaluate risk, and execute an ECA, if needed. Additionally, to best operationalize dent ECA investigations, preliminary assessment methods can be developed that aim to answer critical questions and inform the specific circumstances that require ECAs. Both the preliminary and full process development for understanding the potential threat of dents and other mechanical damage represent new workflows and integrity risk mitigation considerations for gas pipeline operators.
Optimizing the ECA process
ECAs provide a mechanism to calculate the remaining strength of a pipeline based on known inputs such as threats, loadings, operational circumstances, mechanical and fracture material properties, and degradation processes, thus giving operators the information needed to understand the health of their assets.
Performing an ECA for each anomaly in a pipeline is one method of evaluating the effects of dents and mechanical damage on the overall integrity of the pipeline system, which may be necessary in certain circumstances. Alternatively, given the complexities of extensive pipeline systems, operators can also implement expedient methods of assessing or screening anomalies before performing a full ECA in accordance with 49 CFR 192.632.
Methodologies can be designed that are based on codified standards such as API 579-1/ASME FFS-1 - Fitness-For-Service (FFS) to help provide a preliminary assessment and foundation for prioritization. By developing a preliminary ECA assessment methodology, sensitivities to inputs and conservatism can be evaluated to employ the appropriate level of analysis for the associated level of risk. This approach not only targets threats in a risk-based fashion but can be specifically developed so that operators can incorporate their unique system attributes, threats, and risk profiles.
For example, an operator can leverage codified approaches (API 579-1/ASME FFS-1) to prioritize pipeline segments based on failure severity, i.e., propensity for rupture (rather than leak). This effort systematically leverages material properties (e.g., pipe grade, CVN), pipe characteristics (OD, WT, etc.), and operational inputs (MOP) to determine the relative propensity for rupture of one pipeline segment compared to others in the transmission system.
Depending on the system, the unique combination of these factors creates different risk profiles for different threats. This approach allows an operator to focus inspections and integrity assessments on the highest-risk pipelines considering the severity of a potential failure, as well as location, segment length, and operational management decisions.
Similar approaches can be adapted to help operators screen and identify the highest-risk dents and mechanical damage in a pipeline system, thereby characterizing the anomalies that represent stress risers or other "integrity impacts" consistent with PHMSA's updated requirements.
Evaluating risk, preventing failures
Maintaining pipeline integrity is crucial to preventing incidents and reducing impacts to public safety, the environment, and the cost of failures.
Operators will need to have the ability to perform analyses of dents and other damage, including ECAs, sensitivity studies, and risk ranking to meet the requirements outlined by the new regulations. Properly examining, analyzing, and repairing damaged pipelines can reduce the number of pipeline incidents and their associated costs. Formulating processes and procedures to examine pipeline integrity can support operators in minimizing failures and meeting PHMSA requirements.
What Can We Help You Solve?
Exponent's multidisciplinary oil and gas industry experts — including metallurgists, materials, corrosion, mechanical, and thermal specialists — partner with pipeline operators to understand integrity management assessment methods, limitations, input data, and the overall process for optimizing asset safety.
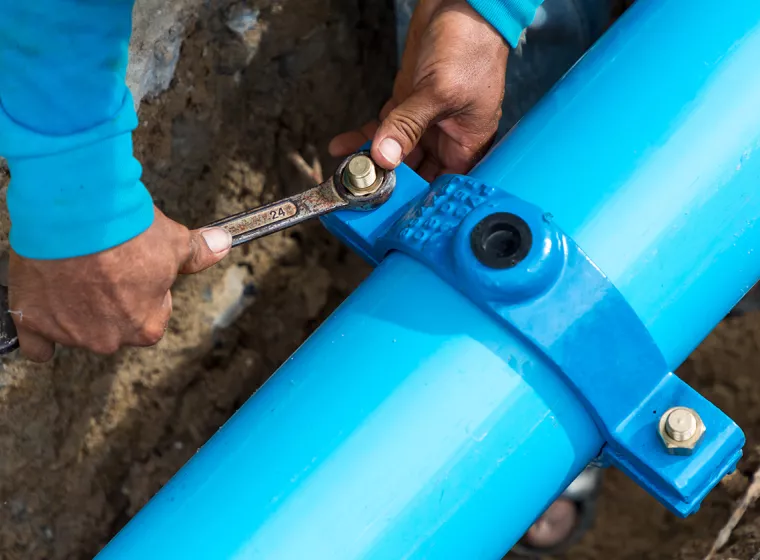
Pipeline & Process Piping
Mechanical engineering expertise for pipeline construction, pipe corrosion, pipeline integrity management, and pipeline failure analysis.
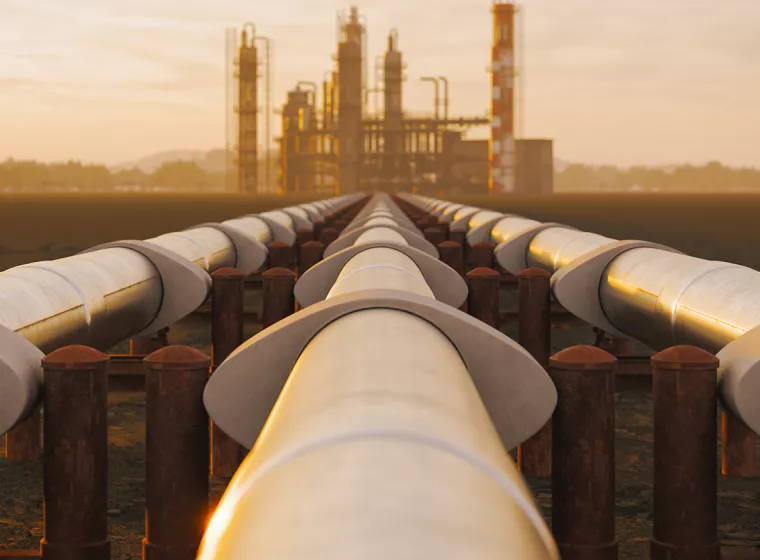
Oil & Gas Pipelines
Multidisciplinary support for oil and gas pipeline challenges at every point in your asset lifecycle.
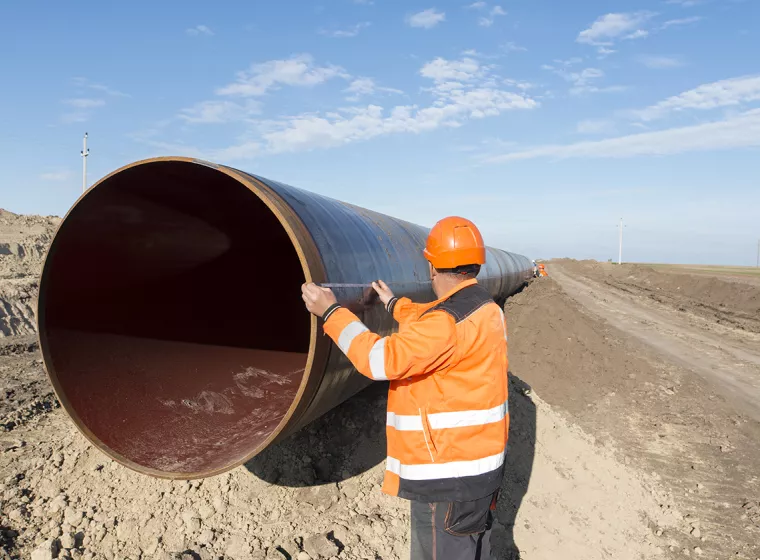
Materials & Corrosion Expertise for Pipelines and Process Piping
Minimize pipeline and piping failures with integrity and pipeline risk assessments.
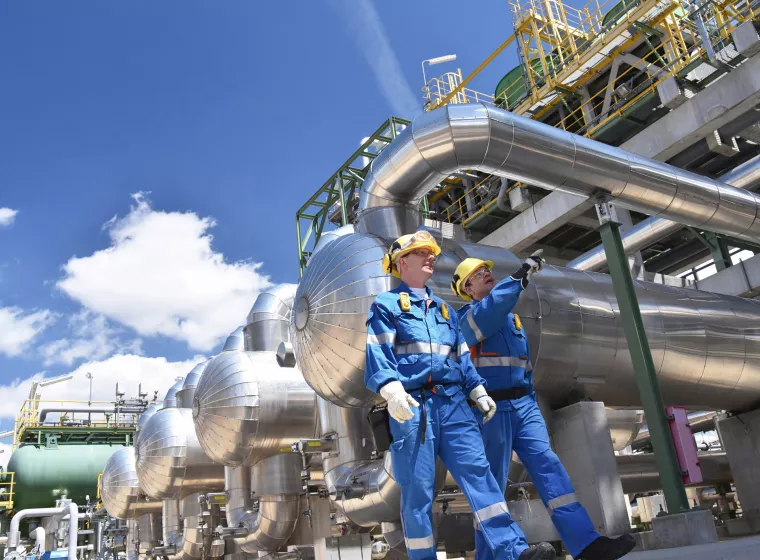
Gas Pipeline Blowdown Risk Assessment
Manage pipeline blowdown hazards with modeling, risk assessment, and process safety advising.
![Liquefied Natural Gas (LNG) [TS]](/sites/default/files/styles/cards_home_card/public/media/images/GettyImages-854095408.jpg.webp?itok=hoWL7ZTm)
Liquefied Natural Gas
Consulting services for the safe handling, transportation, and storage of liquefied natural gas (LNG).
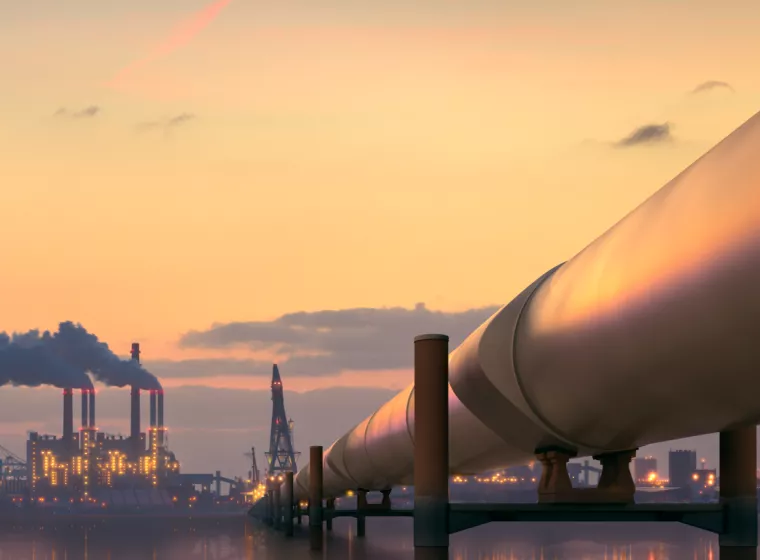
Polymeric Materials Used in the Oil and Gas Industry
Optimize the performance of polymer materials used in oil and gas.