May 26, 2022
Identifying and managing risk for hydrogen blending in natural gas pipelines
Currently, there are at least 26 hydrogen pilot projects being developed by natural gas utilities in the United States, with the potential to address fluctuations in renewable power generation and reduce greenhouse gas emissions.
For example, injecting blue hydrogen produced through steam reforming or green hydrogen produced through electrolysis into natural gas pipelines at percentages of typically 5-10% (potentially up to 20%) can generate power with lower carbon emissions than using natural gas alone. Any upfront costs from blending could conceivably be offset by a credit system similar to that for renewable energy in the electricity sector.
However, there can be complex engineering challenges associated with safely transporting natural gas blended with hydrogen over approximately three million miles of U.S natural gas pipelines.
Because hydrogen can easily diffuse through metal surfaces, some metal pipes used for transporting natural gas may degrade when exposed to hydrogen, particularly at high temperatures and pressures, leading to cracking or pipeline embrittlement.
Hydrogen is also a much smaller molecule than the methane in natural gas, so its leakage rate through pipe walls and joints may be greater, raising economic and safety concerns. And there is no quick test to determine whether a pipe might become compromised because hydrogen damage mechanisms can take a long time to manifest.
How can municipalities, utilities, and other stakeholders determine what blend of hydrogen their natural gas pipelines can safely handle? Armed with precise knowledge of their pipeline systems, as well as an accurate risk assessment and gap analysis, pipeline network owners and operators may be able to safely blend in hydrogen to reduce the carbon footprint of the energy they supply.
Understand the existing piping network
Existing natural gas networks have been designed for natural gas. Blending hydrogen into natural gas lines can affect durability due to factors including pressure, temperature, stress, corrosion, materials composition, and pipeline age. For instance, a pipeline operated under fluctuating pressures may be more sensitive to failure than a pipeline of the same material operated under constant pressure. Consequently, the appropriate hydrogen blend concentration may vary significantly between — and even within — pipeline network systems.
Before network providers and operators can evaluate their own systems and mitigate risks, they need to have a thorough and accurate understanding of the type, capacity, length, size, and construction materials of all the components in their pipeline network. In evaluating pipeline systems, some key considerations include:
Pipeline type: How durable is the system? In the U.S., the Pipeline and Hazardous Materials Safety Administration (PHMSA) requires that operators compile and maintain records indicating what materials, material grades, and types of welds were used for construction. Are these records complete? If steel was used, what are the strength level and maximum hardness of weld heat affected zones?
Welding and heat treatment: Was the pipeline post-weld heat treated? Natural gas pipelines are not typically heat treated after welding, so injecting hydrogen into them could potentially create cracks in areas of high stress at the welds.
Elastomeric components: Does the pipeline include many plastic parts? While polymer-based components, such as mechanical coupling seals and gaskets, flange seals, valve seats, etc., may be compatible with natural gas, they may leak when exposed to hydrogen because it diffuses through certain plastics faster than methane. The materials may also become brittle and fail because they are incompatible with hydrogen.
Consistent with PHMSA requirements, developing documentation for a pipeline network includes a comprehensive review of all as-built design and construction documentation. Incomplete documentation may warrant additional analysis of the pipeline network including using non-destructive examination (NDE) techniques in the field to determine material properties such as microstructure, hardness, chemical composition, and strength.
Examples of NDE methods include ultrasonic contact impedance to characterize pipe hardness and predict tensile strength and instrumented indentation testing (IIT) to verify mechanical properties. Utility providers and other stakeholders with more complete documentation and more confidence in the material properties of their pipeline may only need to conduct NDE on a relatively small portion of their network. Others may need to conduct more rigorous NDE, even up to 100% of their pipelines and components.
Hazard review: identifying risk tolerance
PHMSA currently requires operators to evaluate the integrity of their pipelines in the context of existing requirements. As they consider transitioning to a hydrogen into natural gas blend, operators should also determine the range of hydrogen concentrations and pressures in their natural gas system that present a tolerable risk by combining the likelihood of a loss of containment incident with the severity of the consequences.
Likelihood of an incident
Knowing the materials in their pipeline can allow an operator to identify the likelihood of an incident by ranking which components of their network are incompatible with hydrogen service. For example, higher strength steels can be more susceptible to hydrogen embrittlement. Therefore, mild steel sections of transmission pipelines or sections fabricated using appropriate post-weld heat treatment will potentially have a lower probability of failure than pipelines composed of higher strength steels or non-post-weld heat treated steels.
Other factors, including but not limited to the age of the pipeline, cathodic protection, environment, and intended service, should also be considered when assessing the likelihood of a future incident.
Severity of an incident
After an operator has determined which components in their system are more or less susceptible to failure due to hydrogen exposure, they should assess the consequences of a potential incident, including its impact on people, the environment, and the operator's assets and reputation. A low-severity incident may involve a small-diameter pipe with limited gas flow and pressure in a rural environment. A failure in this line may only cause a small leak that is quickly isolated and repaired with a brief service interruption.
In contrast, a high-severity incident may involve a large-diameter pipe with high gas flow and pressure in an urban environment near an ignition source, such as an electric transmission line. A failure in this line may cause a catastrophic explosion that harms people and the environment and results in irreparable damage to the operator's reputation and ability to conduct business.
Gap analysis: managing risk
After an operator understands the likelihood and severity of a loss of containment incident, they can risk-rank sections of their network to determine whether any modifications must be implemented before hydrogen can be injected into the pipeline. Gap analysis compares the installed equipment capabilities with the minimum specifications for operation with the desired hydrogen blend.
Currently, there is no recognized standard for pipelines that convey blends of hydrogen and natural gas. Therefore, operators should determine whether their pipelines should comply with ASME B31.8 Gas Transmission and Distribution Piping Systems (which applies to natural gas), ASME B31.12 Standard on Hydrogen Piping and Pipelines (for pure hydrogen), or a combination of these standards. These standards contain requirements covering areas such as materials, metallurgical characteristics, brazing, welding, heat treating, forming, testing, inspection, examination, operating, and maintenance.
Without a recognized standard for pipelines that convey blends of hydrogen and natural gas, operators may elect to conduct a gap analysis between the piping and components in their current network against the relevant requirements of ASME B31.8 and ASME B31.12 as part of their risk assessment. Operators might determine that sections of their system compliant with both standards are at a lower risk of an incident, while sections not compliant with ASME B31.12 are at a higher risk and require modification before hydrogen injection. Operators might be required to reduce the amount of hydrogen injected, decrease the system pressure, or remove the pipeline from service until appropriate modifications are made to reduce the risk to a tolerable level.
How Exponent Can Help
Exponent's thermal sciences, metallurgy, and corrosion team has extensive experience evaluating hydrogen technologies. We can offer possible solutions to integrating and implementing hydrogen technology across applications. Through our deep knowledge of industry standards and best practices, we can develop a customized plan for conveying a blend of hydrogen and natural gas that is specific to each client's pipeline network using techniques such as risk assessment for pipeline operation and transition, gap analysis, advanced NDE, and metallurgical studies to examine corrosion and embrittlement.
What Can We Help You Solve?
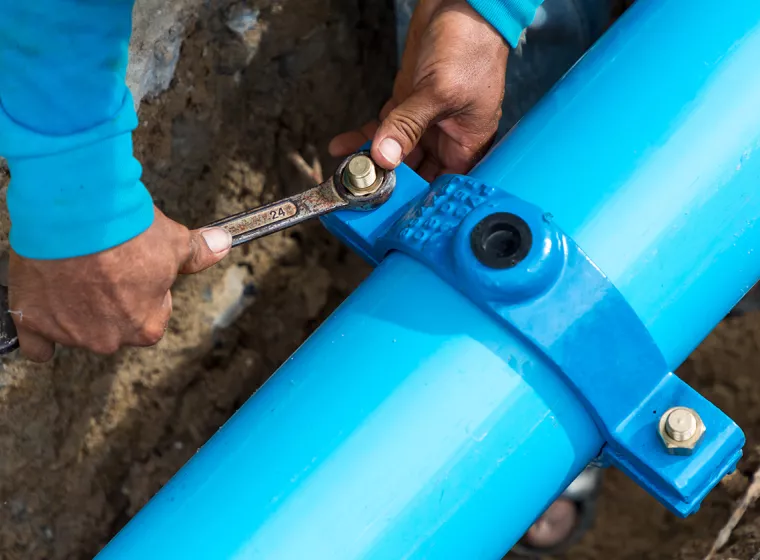
Pipeline & Process Piping
Mechanical engineering expertise for pipeline construction, pipe corrosion, pipeline integrity management, and pipeline failure analysis.
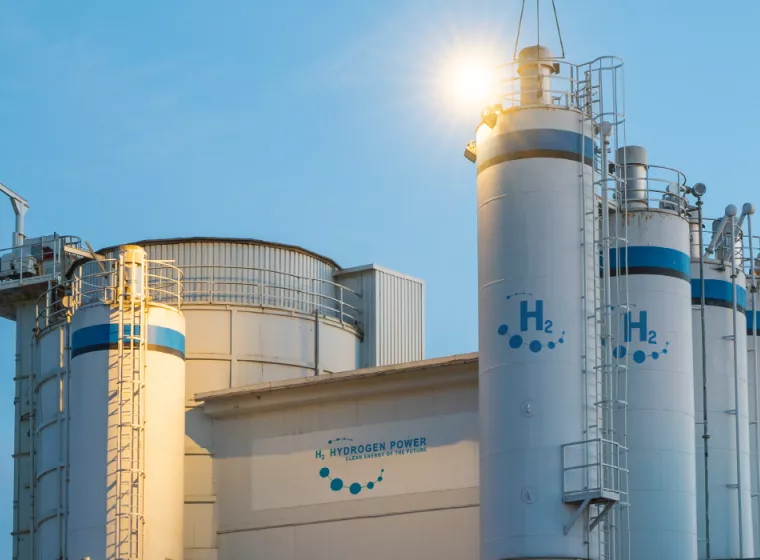
Hydrogen Systems & Fuel Cell Technologies
Innovate with new hydrogen technologies and solve challenges with electrolyzers, fuel cells, liquefaction technologies, and ammonia conversion systems.
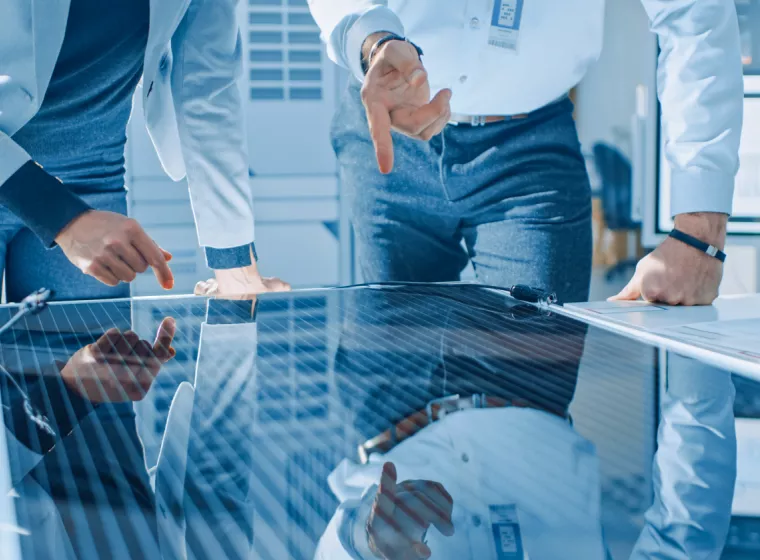
Thermal Sciences Expertise for Energy Systems
Energy systems design, safety, and compliance consulting across a range of industries, including oil and gas, renewable and utility power generation.
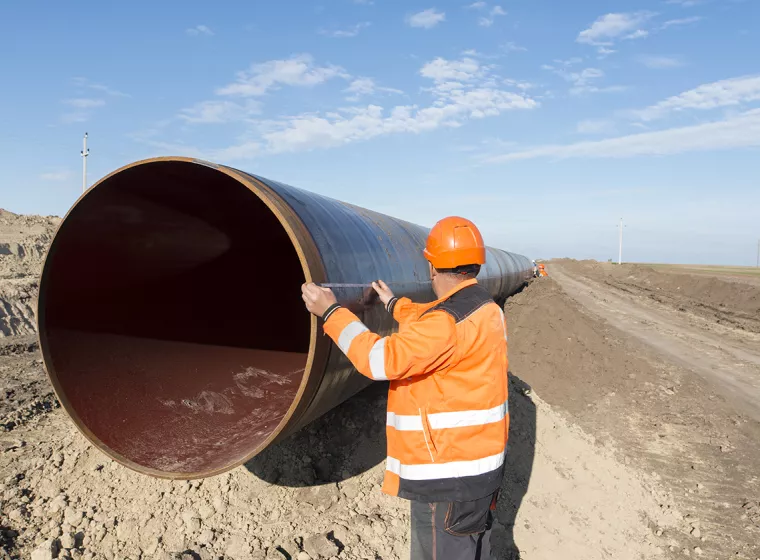
Materials & Corrosion Expertise for Pipelines and Process Piping
Minimize pipeline and piping failures with integrity and pipeline risk assessments.