The Challenge
A contractor specializing in factory automation was hired to design and construct an automated assembly line for installing flooring in cargo containers. The as-designed equipment was unable to meet production speed and quality specifications, and the project fell massively behind schedule.
The purchaser partially and then fully canceled the contract and shortly thereafter exited the container business altogether.
A dispute arose as to whether the failures to meet specifications and schedule were due to engineering errors on the part of the contractor or were due to the purchaser's failure to supply appropriate and timely materials for testing. The contractor also asserted that, if not for these material defects, it would have completed the project per the contract time schedule.
Claims were submitted to arbitration by a one-member tribunal under London Court of International Arbitration (LCIA) rules.
The Exponent Approach
The cargo container manufacturer's outside counsel retained Exponent to assess the design basis for the assembly line, review the test materials supplied by the manufacturer, perform a schedule and delay analysis, and assess the project cost allocations.
Exponent's team submitted separate expert reports and rebuttal reports on both the technical and schedule/quantum issues, prepared to give expert evidence on behalf of the manufacturer, gave counsel tutorials on the technological issues, and participated in a joint-expert conference and statement.
The parties reached a settlement shortly after and days before the arbitration was scheduled to begin.
Insights
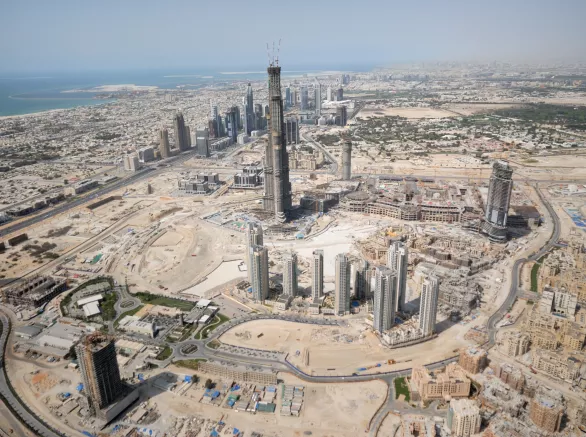