October 31, 2024
Commercial-scale direct lithium extraction technologies present big opportunities for the battery industry — with big challenges still ahead
Surging demand for electric vehicles and grid-scale energy storage are key drivers of what some are calling the "white gold" rush — the global race to source and refine lithium to feed the world's growing appetite for lithium-ion batteries. According to Columbia University's Center on Global Energy Policy, demand for lithium has tripled since 2017, and it's expected to increase tenfold by 2050, resulting in a likely shortage as soon as the 2030s.
Concerns over lithium's environmental costs — including production processes that generate significant carbon dioxide emissions and consume staggering water resources — have many stakeholders considering new battery chemistries. However, with some of the most promising contenders (solid-state, silicon-anode, sodium-ion) still in development, and Li-ion batteries commercially established, alternative lithium sourcing practices that are more environmentally friendly are gaining traction, including direct lithium extraction (DLE) technology.
As U.S. regulatory momentum — led by the Biden Administration's Inflation Reduction Act — grows around securing diversified, domestic, and sustainable sources of lithium and other critical minerals, the application of DLE to geothermal and oilfield brines across the U.S. could represent a significant shift from conventional lithium harvesting methods practiced in Australia, Chile, and China. For DLE to reach its full potential, however, manufacturers and other industry stakeholders will have to first overcome key regulatory, legal, financial, and technological challenges.
The potential benefits of DLE
While lithium has historically been produced through open-pit surface and underground rock mining techniques, today, almost two thirds of the world's supply is produced from brine evaporation ponds. This method involves drilling subsurface rock formations to reach brine aquifers, pumping brine into surface ponds, a lengthy water evaporation process, and filtering out concentrated lithium salts. It also requires approximately 500,000 gallons of water or more a year to extract a single ton of lithium.
DLE, on the other hand, does not involve evaporation ponds, rock mining, or the associated water waste and carbon emissions. One key advantage of DLE is that after pumping the brine to the surface, the water is subjected to direct extraction — by mechanical or electrochemical processes — after which any treatment water or unused brine is injected back into deep subsurface formations, well below useable sources of drinking water.
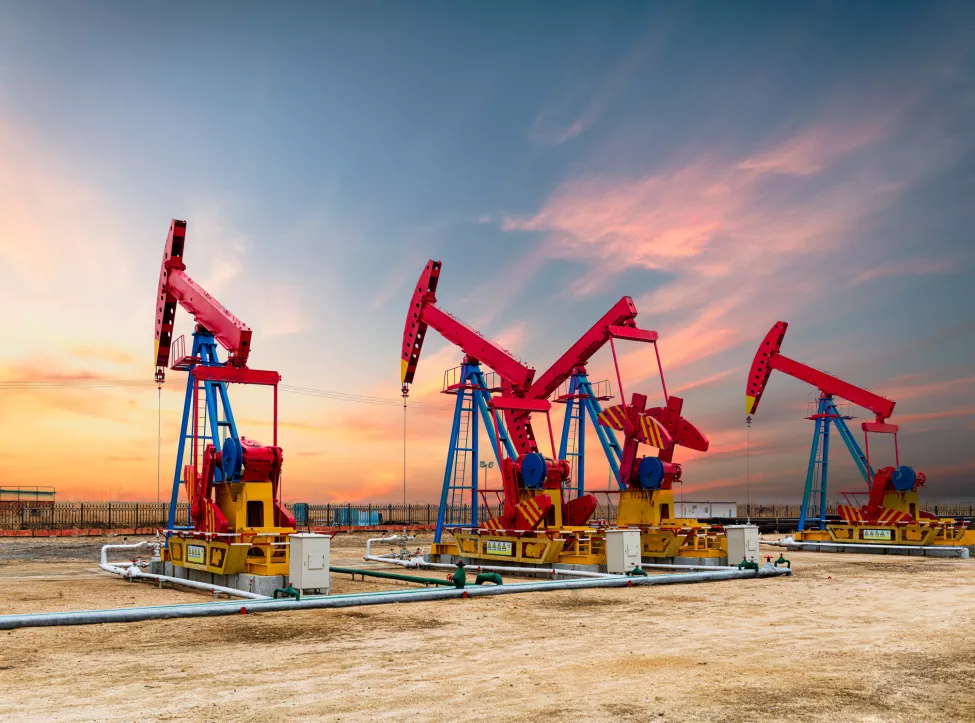
Applying DLE to domestic oil and gas wells and geothermal projects
The promise of DLE extends beyond lithium harvesting from dedicated brine production wells. The same DLE techniques can be used to extract lithium from the so-called "produced water" from oil and gas wells and the brine from geothermal energy generation, products otherwise considered industrial wastes.
Produced water — which contains hydrocarbons, salts, a variable mix of additives, and other solids and substances, including lithium — is fluid with gas and oil that, once extracted during normal production processes, is typically either injected back underground or recycled for future hydraulic fracturing operations, and which, with the application of DLE technology, represents a new resource for lithium sourcing. Shale in the Appalachian Basin, including Pennsylvania's Marcellus shale formation — the largest reserve of natural gas in the U.S. — is particularly rich in lithium, with promising implications for domestic lithium production through DLE. A 2024 study in the journal Scientific Reports estimated that produced water from the Marcellus Shale formation alone could satisfy 40% of current U.S. lithium consumption, and other regions like the Smackover limestone formation, where large oil and gas companies have begun DLE projects, provide similar cause for optimism.
As part of additional efforts to boost domestic lithium production, the state of California is constructing a DLE facility to extract battery-grade lithium-hydroxide during geothermal energy generation at the Salton Sea, in this case resourcing deep brine ponds (and their lithium salts) exposed in the course of drilling through fractured hard rock formations.
Challenges ahead for DLE implementation
Despite DLE's potential, battery manufacturers, multinational oil and gas operations, and other minerals and energy storage stakeholders face an array of challenges to fulfill the promise of this emergent technology.
Despite technological and regulatory uncertainty, DLE exploration and commercialization is moving rapidly.
The path toward secure and sustainable lithium sourcing
Despite technological and regulatory uncertainty, DLE exploration and commercialization is moving rapidly. Through its Smackover project and other DLE projects worldwide, ExxonMobil has set a goal to supply lithium for more than one million EVs annually by 2030, and Standard Lithium's $225 million in funding from the Department of Energy to construct a commercial-scale extraction and processing facility for battery-grade lithium carbonate represents an unprecedented boost to the modern, domestic production of critical minerals.
And yet, as the "white gold" rush turns to oil and gas brines and geothermal projects for more secure, sustainable lithium harvesting, commercially successful DLE applications will require continued innovation rooted in rigorous scientific analysis. Cutting-edge techniques, such as hydrogeological modeling of lithium brine deposits, and applied scientific and engineering expertise will help industry fulfill DLE's promise to reduce the resources required to source this key component of the world's energy future.
What Can We Help You Solve?
Exponent has decades of experience helping energy companies, mining operations, and battery manufacturers solve complex technological and regulatory challenges. Our experts in geochemistry, petroleum and reservoir engineering, battery engineering, geosciences, environmental engineering, supply chain analysis, and regulatory compliance deliver rigorous evaluations and breakthrough insights to accelerate innovation, mitigate risk, and speed time to market.
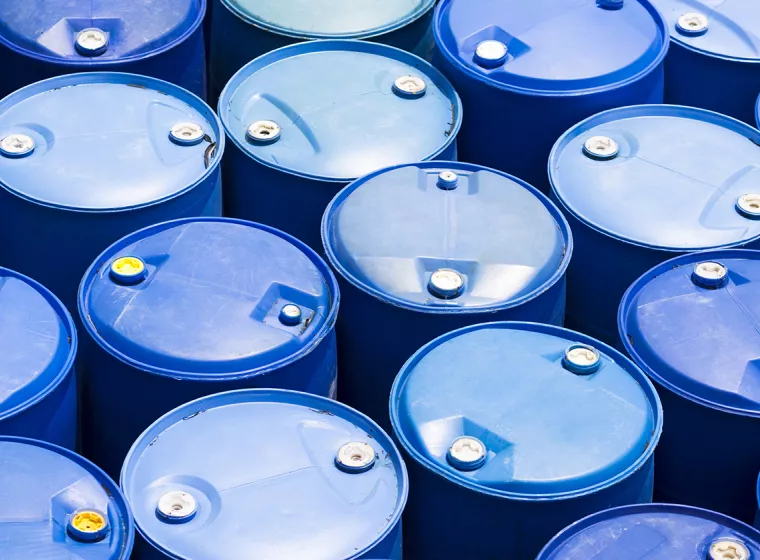
Chemical Engineering
Extensive production and safety assessments for facilities combining hazardous and reactive materials, novel technologies, and interconnected equipment.

Batteries & Energy Storage
Supercharge performance, reliability, and safety across all stages of the battery and energy storage product lifecycle.
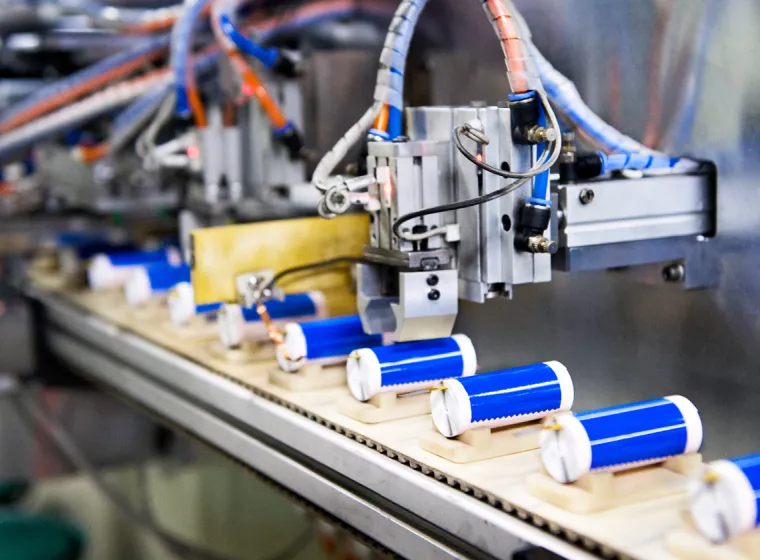
Battery Supply Chain Services
End-to-end battery supply chain support including evaluating potential manufacturer partners and suppliers

Environmental Permitting
Extensive support for compliance with local, state, and federal permitting requirements.
![[EBS] Ecological & Biological Sciences - Environmental Risk Assessment - grey heron grazing in fresh water](/sites/default/files/styles/cards_home_card/public/media/images/grey-heron-2022-01-04-23-54-37-utc%281%29_0.jpg.webp?itok=5EB0lXjA)
Environmental Risk Assessment
Risk assessments for legacy spills and contamination, potential project and product impacts, and environmental remediation support.
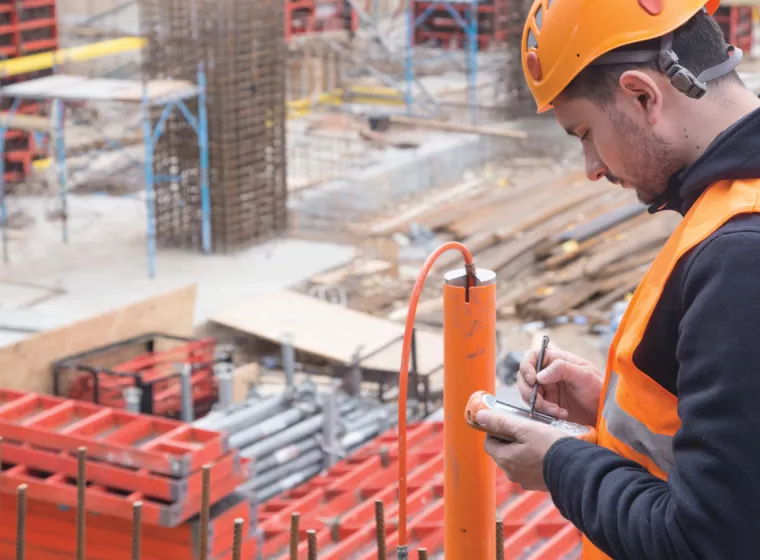
Geotechnical Instrumentation & Monitoring
Geotechnical instrumentation monitoring services tailored to specific applications and needs at every stage of a project lifecycle.